Pneumatic actuators have emerged as an important component of the majority of the higher pressure applications owing to their efficiency and ability to withstand exceptionally severe working conditions. From oil and gas production to chemical manufacturing and even power generation, pneumatic actuators enhance the overall system functionality by granting smooth and precise control over the valves even in extreme conditions. This article will discuss the reasons why these actuators are best suited for systems operating at high pressure, their performance efficiency, the advantages they provide, and, most importantly, why the system’s efficiency can be further improved by partnering with trustworthy valve manufacturers in the USA.
Defining Pneumatic Valve Actuators
Pneumatic valve actuators are devices that automate valve operations on the basis of compressed air. These pieces of equipment are used with automation systems that need quick and dependable controlled movements. In worst case scenarios, where electricity will not be accessible, pneumatic devices tend to be more dependable in comparison to hydraulics or electrics. The versatility in the pneumatic device tends to make the components less complex giving them an advantage in areas which require power generation and chemical Industry manufacturing. These factors along with high pressure durability and ease of maintenance makes them an ideal approach in the case where there is a high risk and more importantly maintaining precision and speed is crucial. In contrast, using other sources of movements such as electric or hydraulic systems come with more complex components which are prone to fail more easily. With a pneumatic system, a user does not need to worry about constantly servicing it. This leads to greater efficiency especially in situations of high volume and high risk scenarios.
Durability and Reliability in High-Pressure Systems
Pneumatic actuators have long been considered “the workhorse” of industries owing them extraordinary utility. In high pressure settings, these systems exhibited unparalleled capabilities. Unlike hydraulic actuators which create force through fluids, pneumatic actuators depend on compressed air. The higher the pressure, the lower the chance of leaking or contamination. This facilitates the lowering of breakdown rates in specific industries that have constant fluctuations in pressure like chemical processing, petroleum refining, and heavy production systems. Another major advantage of pneumatic actuators comes in the form of having reduced moving parts in comparison to the hydraulic counterpart. This helps decrease chances for mechanical breakdown. Incorporating corrosion resistant materials into the design of pneumatic actuators enhances their ability to operate in extremely harsh and high pressure environments. This makes them highly reliable. Since the actuator system does not depend on any hazardous fluids, the risk of spilling and leaking damaging equipment or posing danger to personnel is eliminated. This improves the overall cost efficiency and safety of the operations. Furthermore, the simplicity of design negates the need for maintenance which increases operational window time reliability, especially in challenging scenarios, along with giving operators peace of mind.
Prompt Reaction Capacities and Reaction Control
The rapid response and accurate control of changing parameters is critical while operating in high-pressure conditions. When comparing different actuators, Pneumatic actuators provide faster response times when compared to electric or hydraulic actuators. Their speed is particularly valuable in applications where rapid adjustments are necessary to maintain system stability. For instance, the actuator in a high-pressure steam control system has to address the pressure changes in the system very quickly to avoid fatal over-quenching. In addition, pneumatic valve actuators allow for great accuracy in controlling the valve opening so that the pressure is kept at the desired value without large oscillations. Such precision is critical for the effective control of critical processes, along with ensuring operational safety in systems used in oil and gas industries, where the pressure level has to be set at an optimum value to ensure safety and operational effectiveness. The responses of pneumatic actuators to pressure variations can be regarded as instant, which enhances system efficiency by reducing the chances of pressure build-up or stochastic operations. This promotes better system performance, which is of utmost importance in high-pressure settings where even the slightest change could result in system damage or impairment.
Why Trust a US Based Valve Manufacturer?
Considered to be one of the reliable usa valve manufacturers, trusted shield stands out when it comes to producing high quality and innovative actuator solutions. Similar to any other known valve manufacturing company, an order can be placed for anything ranging from challenges such as durable pneumatic valve solutions that allow for efficient performance in highly demanding applications. Most established industry leaders do not have to worry about reputable suppliers because having a dependable supplier seals the deal when it comes to industry standards for pressure thresholds or strict regulations when it comes to durability and safety. It also ensures a steady source of ongoing technical support and timely product delivery which helps mitigate any unnecessary challenges. Shield flow technologies is one of the many manufacturers that proactively understand local regulations and industry standards. They incorporate feedback that is unique to each customer’s requirements while providing fine-tuned feedback that meets defined instructions. In fact specialists serving valve automation control and industries on the other side of the spectrum value the ability to instantly receive localized custom components at short notice and minimal cost.
Conclusion
As a result, it is clear that pneumatic valve actuators have the most benefits on high-pressure systems in terms of custom energy efficiency, robust construction, reliability, and responsiveness to demands. It is fundamental for such industries as oil and gas, chemical processing, or power generation to maintain critical pressure levels because these tasks are performed in extreme environments. For these reasons, businesses can guarantee that partnering with reputable valve makers in the United States enables them to leverage the most appropriate pneumatic actuator innovations for their challenges. In addition to providing high-quality products, pneumatic valve suppliers offer expert advice and maintenance services, ensuring that high-pressure systems run smoothly and efficiently. Furthermore, the evolution of automation within industries and their increased expectations will ensure that the industry is not deprived of pneumatic valve actuators which augment the measure of security and operational efficiency during intensive work. Modern pneumatic valve actuators are the key sensitive elements of industrial automation because they function under severe conditions, accurately and reliably control, and ensure the efficient operation of high pressure systems.
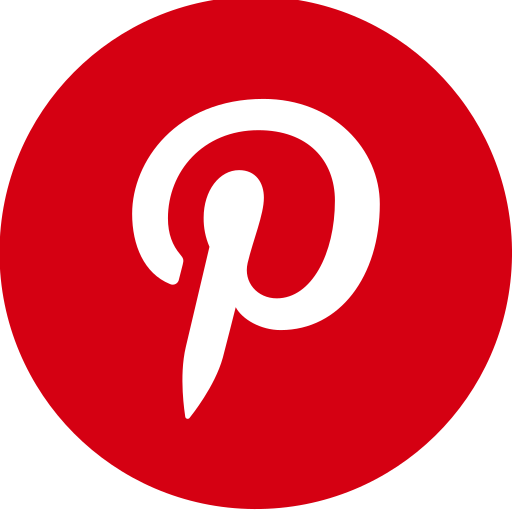