The ability to weld is a talent that is absolutely necessary for those who work in the construction and industrial segments of the economy. It is a significant technique that is used in the process of fusing metal components together in order to manufacture a wide range of different kinds of constructions and products.
One of the most essential components of shear stud welding machine manufacturers is the electrode, which is one of the most useful components. There is a significant difference that can be brought about in terms of the quality of the weld as well as the ease with which the welding process can be performed if the suitable electrode is used.
This article will cover the fundamentals and workings of welding electrodes.
- Electrodes used in welding are an important component of the welding process. They perform the function of filler material, which is responsible for joining two pieces of metal together. In order to create welds that are strong and long-lasting, it is essential to have a fundamental understanding of welding electrodes.
- When choosing a welding electrode, the material composition of the electrode is one of the most important elements to take into consideration. For use with certain kinds of metals, such as mild steel, stainless steel, or aluminum, several electrodes have been developed specifically for use with those metals. In order to achieve effective fusion and reduce the likelihood of errors in the weld, it is important to choose the appropriate electrode material.
- In addition, the diameter of the welding electrode is a crucial factor that takes into consideration when calculating the size of the weld bead and the level of penetration. While thinner electrodes are good for welding thin metals, thicker electrodes are appropriate for welding thicker materials or generating deeper welds. Thinner electrodes are best for welding thicker materials.
What Is The Operation Of Welding Electrodes?
During the process of welding on a particular metal joint, the current travels from the machine to the electrode holder, which is grounded in the area where the welding is taking place. A metal bead is produced as a consequence of the electrode being heated up and melted by the process. Because of the decrease in temperature, the bead becomes more solid, which causes the metal to bond together.
To put it another way, welding is the technique of putting together components made of metal at the same time. The joining of metal may be accomplished by a number of different techniques, such as brazing, soldering, and riveting. Welding, on the other hand, has become more popular due to the fact that it is robust, versatile, and effective.
Now that you are familiar with what welding electrodes are and how they function, it is time to learn about the two primary kinds of welding electrodes and the many professional applications for each of them.
- Electrodes that are Depletable
A consumable electrode or welding rod performs exactly the same function as its name suggests. When you use these filler electrodes to weld a joint, the rods melt and are consumed in the process of bridging the gap between the parent metal and the other metal portion. This is because the rods are used to bring the two metals together. Stick electrodes and solid wires are two examples of frequent examples of welding consumables.
2. Non-consumable electrodes
On the other hand, a non-consumable electrode does not undergo any changes in its characteristics and does not melt throughout the process without undergoing any changes. It is solely for the purpose of establishing and maintaining the electric arc that such an electrode is used.
It is the fact that non-consumable electrodes are constructed of materials with higher melting points, such as tungsten, graphite, and carbon, that is the source of the mystery that lies behind the solid structure that they have after welding. The non-consumable rods, on the other hand, are susceptible to deterioration over time as a result of erosion or vaporization.
3. Hardfacing Electrodes
In surfacing applications, hardfacing electrodes are used in situations where the welded surface must be resistant to wear and abrasion. The mining industry, the construction industry, and the agricultural industry are all popular application areas for these electrodes.
4. Electrodes made of stainless steel
Another top-selling product that may be offered from is a ready-to-use pack of stainless-steel electrodes for shear stud welding machines. These electrodes are designed to ensure a constant weld quality regardless of the influence of temperature and weather.
Conclusion
Thus, you may improve your welding abilities and get consistently high-quality welds by knowing how to handle and various kinds of welding electrode difficulties. Welders can select the most appropriate electrode for each welding project.
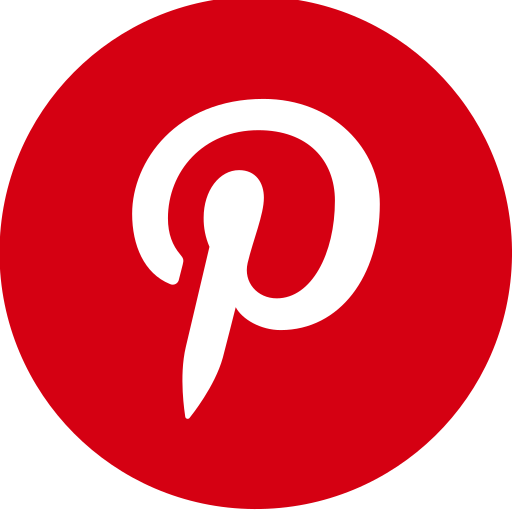