Two elements every startup seeks during their product development journey. When you’re racing to bring a concept to market before the competition, time is more valuable than gold. That’s where 3D modelling steps in- not just as a visual tool but as a transformative solution that turns napkin sketches into market-ready products.
Gone are the days when prototyping involved hefty manufacturing costs, delayed timelines, and excessive guesswork. Now, with 3D modelling, startups can visualize, iterate, and refine designs long before committing to physical production. It empowers founders, engineers, and investors with clarity and control over the entire product lifecycle.
Let’s explore how 3D modelling is helping startups prototype faster and smarter- and why it’s becoming a non-negotiable tool for innovation.
Improved Communication Between Designers and Developers
One of the most significant hurdles during product development is miscommunication. Traditional sketches often fall short in conveying detailed design intent. That’s where 3D modelling bridges the gap.
Benefits of enhanced collaboration:
- Visual clarity ensures developers understand precise dimensions and material specifications.
- Stakeholders can explore the model from every angle for better alignment.
- Fewer revisions are required as the design intent is made clearer from the start.
Using 3D modelling, teams avoid costly misunderstandings and improve the efficiency of the development process.
Cost Reduction by Minimizing Physical Prototypes
Physical prototypes are expensive, especially when revisions are frequent. 3D modelling allows startups to simulate multiple design alternatives digitally before investing in a tangible version.
Instead of building five different prototypes to test variations, a startup can digitally create all five, run simulations, and identify the most viable option. The cost savings from materials, labor, and production downtime are significant.
3D modelling transforms prototyping from a guessing game into a data-driven process.
Precision Engineering with Parametric Design Tools
Startups building hardware need more than creative ideas- they need technical precision. That’s why 3D modelling platforms like SolidWorks, Fusion 360, and Rhino are critical.
These tools allow for:
- Parametric control (automated dimension adjustments)
- Tolerance testing for real-world feasibility
- Integration with 3D printing platforms for direct prototyping
By leveraging 3D modelling, even small teams can match the precision of enterprise-level product development.
Faster Stakeholder Buy-In with High-Quality Visuals
It’s one thing to explain a concept. It’s another to show it. Visuals created through 3D modelling help startups impress stakeholders, secure investments, and gain early feedback.
Instead of flat 2D blueprints, startups can pitch using:
- High-resolution renderings
- Interactive 360° product viewers
- AR previews using mobile apps
These immersive assets build confidence and communicate vision far more effectively than static slideshows.
Streamlined Testing Through Digital Simulations
Testing is a major bottleneck. But digital simulations powered by 3D modelling now offer predictive insights without needing physical tests every time.
Startups can simulate:
- Heat resistance
- Material stress
- Mechanical function under pressure
With these tests integrated directly into modelling software, errors can be caught early—before real-world flaws cost time and money.
Customization at Scale Without Additional Costs
Modern consumers crave personalization. And thanks to 3D modelling, startups can offer customization at scale without significant overhead.
Using modular templates and parametric inputs, a startup can build product variants for different markets or customer segments. For example:
- A wearable startup can adjust strap sizes for different users.
- A furniture brand can create modular designs for different room sizes.
These variations no longer require separate molds or manufacturing lines—just smart modelling.
Rapid Prototyping through 3D Printing Integration
Perhaps the most tangible benefit of 3D modelling is its seamless integration with 3D printing technologies. Digital designs can now be printed within hours, allowing teams to:
- Validate form factors
- Test ergonomics
- Confirm assembly fit
This is especially useful for hardware startups that want to go from digital to physical without manufacturing delays.
Better Version Control and Design Iteration
Startups often pivot. As products evolve, keeping track of design changes is vital. 3D modelling tools come with built-in version control, making it easy to:
- Revisit old iterations
- Track performance improvements
- Collaborate on changes remotely
This organized workflow helps growing teams manage complexity and avoid rework.
Stronger Branding with Photorealistic Product Renderings
A product’s first impression often comes from its image- not its performance. With 3D modelling, startups can create photorealistic renderings for marketing, crowdfunding, and website use long before the actual product is ready.
Why this matters:
- Speeds up go-to-market strategies
- Enables pre-orders with real visual appeal
- Provides marketing teams with high-quality visuals from day one
3D modelling isn’t just for engineers- it’s a tool for storytelling.
To Wrap Up
3D modelling has evolved into far more than a design tool. For startups, it’s the heartbeat of innovation—speeding up development, cutting costs, and bringing ideas to life with precision and clarity.
From enabling real-time feedback to empowering lean hardware teams, its influence spans across prototyping, testing, branding, and marketing. Startups that integrate 3D modelling early in their workflow gain a competitive edge and are better equipped to iterate, pivot, and scale.
Hire Outsourced 3D Modelling Services through Invedus Outsourcing – Seamless Platform to hire.
Read Our Recent Blog – Why Companies Outsource 3D Modeling for Faster Product Development
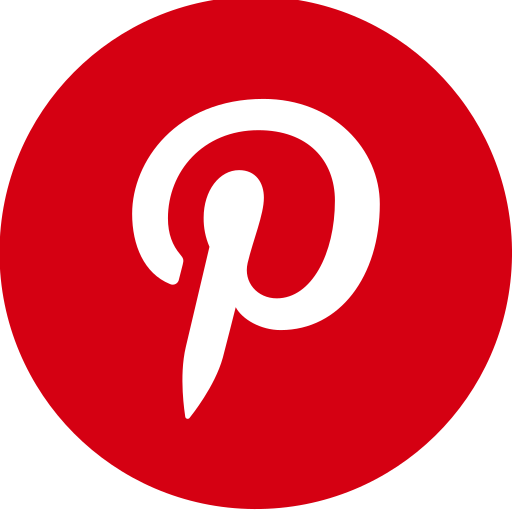