The global chemical industry plays a critical role in the development of many products that are essential to daily life, ranging from pharmaceuticals to industrial applications. Oleum, a key industrial chemical, is used extensively in the production of sulfuric acid, as well as in several chemical processes across industries such as textiles, detergents, and petroleum. For investors, entrepreneurs, and companies looking to enter the oleum market or expand their existing operations, an Oleum Manufacturing Plant Project Report is crucial. This report serves as a comprehensive guide for setting up a plant, understanding the costs involved, identifying the top manufacturers, and navigating the feedstock requirements and market dynamics.
What is Oleum?
Oleum, also known as fuming sulfuric acid, is a solution of sulfur trioxide (SO₃) in concentrated sulfuric acid. It is primarily used to produce sulfuric acid on a large scale and also serves as a critical component in other chemical manufacturing processes, such as the production of detergents, fertilizers, and various industrial chemicals.
Request Your Free Sample Report – https://www.procurementresource.com/reports/oleum-manufacturing-plant-project-report/request-sample
Due to its strong oxidizing and corrosive properties, oleum must be handled carefully, which makes its manufacturing process and storage facilities particularly important.
Oleum Manufacturing Process
The process of manufacturing oleum involves the combination of sulfur trioxide and concentrated sulfuric acid. The sulfur trioxide is typically produced by the catalytic oxidation of sulfur dioxide (SO₂) in the presence of oxygen. The reaction occurs at high temperatures, and the resulting gas is absorbed into concentrated sulfuric acid.
The manufacturing of oleum can be broken down into the following stages:
- Sulfur Combustion: The process begins with the combustion of sulfur (S) in the presence of oxygen (O₂) to produce sulfur dioxide (SO₂). This occurs in a furnace under controlled conditions.
- Conversion to Sulfur Trioxide: The sulfur dioxide gas is then reacted with excess oxygen in a converter, usually at high temperatures (450-600°C), in the presence of a vanadium pentoxide (V₂O₅) catalyst. This reaction forms sulfur trioxide (SO₃).
- Absorption of SO₃: The sulfur trioxide gas produced in the conversion stage is then absorbed into concentrated sulfuric acid, forming oleum. This is done in a special absorption tower where the SO₃ gas is dissolved into the liquid acid.
- Oleum Storage and Packaging: Once the oleum is produced, it is typically stored in specially designed tanks that can handle its corrosive properties. Oleum is available in various concentrations, depending on the desired sulfuric acid production or industrial use.
Cost Model for an Oleum Manufacturing Plant
The cost model of establishing an oleum manufacturing plant can vary significantly based on the scale of production, the location of the plant, feedstock costs, and equipment investment. Typically, the capital investment for such a facility is high due to the need for specialized equipment and safety measures.
Major Cost Components
- Plant Construction Costs: This includes the design, construction, and setup of the oleum production facility. Given the hazardous nature of the materials, specialized equipment such as reactors, absorption towers, and storage tanks are required.
- Feedstock Costs: Sulfur and oxygen are the primary feedstocks for oleum production. The cost of sulfur can vary depending on its source, which can include natural sulfur or byproducts from other industrial processes. The procurement of feedstocks is a key factor in determining the overall operational cost.
- Energy Consumption: The production of sulfur trioxide and oleum requires substantial amounts of energy, both for heating the reactors and for maintaining the necessary temperatures throughout the process.
- Labor and Operational Costs: Skilled labor is essential for the efficient operation of an oleum manufacturing plant. This includes technicians for plant maintenance, operators for chemical reactions, and safety officers to ensure compliance with industrial standards.
- Environmental Compliance and Waste Management: Given the hazardous nature of the materials, environmental considerations such as air filtration systems, waste disposal, and sulfur dioxide recovery are critical. Compliance with environmental regulations can add to the operational costs.
Read Full Report With Table Of Contents: https://www.procurementresource.com/reports/oleum-manufacturing-plant-project-report/toc
Top Manufacturers of Oleum
There are several key players in the oleum manufacturing industry who dominate the global market. Some of the top manufacturers are well-established chemical companies that produce oleum as part of their sulfuric acid production operations.
- BASF: As a leader in the chemical manufacturing space, BASF produces a wide variety of industrial chemicals, including oleum. Their robust infrastructure and extensive research facilities allow them to stay competitive in the market.
- Dow Chemical: Dow is another global giant with an established presence in the production of oleum, especially for applications in the petrochemical and refining industries.
- Hindustan Zinc Ltd: In India, Hindustan Zinc is one of the top producers of oleum, offering it in varying concentrations to meet industrial demands.
- China National Petroleum Corporation (CNPC): CNPC is a major producer of oleum and other chemicals in the Asia-Pacific region, largely due to its integration with oil refining and petrochemical production.
Market Drivers for Oleum
The demand for oleum is driven by a variety of factors, especially in regions with strong industrial bases. Some key market drivers include:
- Industrial Growth: As industries like petroleum refining, fertilizers, and chemical manufacturing grow, so does the demand for oleum. The need for sulfuric acid as an intermediate in the production of fertilizers and other chemicals propels this growth.
- Economic Development in Emerging Markets: Many emerging markets are witnessing industrialization, which is driving up the demand for oleum and sulfuric acid in applications such as oil refining and the production of chemicals.
- Sustainability Focus: Environmental concerns about the use of oleum in sulfuric acid production have led to innovations aimed at reducing sulfur dioxide emissions. This is promoting the adoption of cleaner technologies, potentially influencing the market dynamics.
- Technological Advancements: Technological advancements in the oleum production process, such as more energy-efficient reactors and improved sulfur trioxide absorption systems, have led to cost reductions, which positively affect market growth.
Procurement Resource and Feedstock Requirements
For any business considering the establishment of an oleum manufacturing plant, procurement is a critical component. Securing a reliable supply of feedstocks such as sulfur and oxygen is essential for the smooth operation of the plant. This requires not only establishing contracts with suppliers but also ensuring that transportation logistics are optimized for cost and efficiency.
Additionally, procuring specialized equipment for the production, storage, and transportation of oleum is another essential element of the project. Procurement resource management plays a pivotal role in minimizing costs and ensuring that the necessary materials and equipment are available when required.
Key Insights into the Oleum Manufacturing Market
The global oleum market is poised for growth, driven by increased industrial activity and technological advancements in sulfuric acid production. Companies that are able to optimize their production processes, reduce energy consumption, and comply with environmental regulations will hold a competitive edge in the market.
For investors and entrepreneurs, the key to success lies in understanding the cost dynamics, feedstock availability, and the competitive landscape. By consulting an Oleum Manufacturing Plant Project Report, companies can gain detailed insights into these aspects, enabling informed decision-making and efficient project execution.
The oleum manufacturing industry remains a critical component of global chemical production. With an understanding of the manufacturing process, cost model, feedstocks, market drivers, and procurement resources, companies can effectively navigate this competitive space. For anyone considering entering the oleum market, an in-depth Oleum Manufacturing Plant Project Report serves as an essential tool for outlining strategies, understanding costs, and securing a strong position in the industry.
Contact Us:
Company Name: Procurement Resource
Contact Person: Endru Smith
Email: sales@procurementresource.com
Toll-Free Number: USA & Canada - Phone no: +1 307 363 1045 | UK - Phone no: +44 7537171117 | Asia-Pacific (APAC) - Phone no: +91 1203185500
Address: 30 North Gould Street, Sheridan, WY 82801, USA
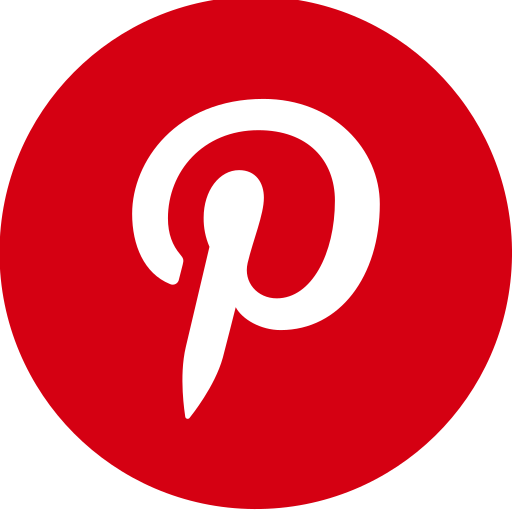