In the intricate world of electronics, custom cable assemblies serve as the lifeline that ensures seamless communication and efficient performance of devices and systems. Tailored to meet specific needs, custom cable assemblies are essential for various applications, from industrial machinery to consumer electronics. When partnering with cable assemblies manufacturers, it’s crucial to consider several factors to ensure that the final product meets all technical and functional requirements. Here, we delve into the key considerations for custom cable assembly and their applications.
Understanding Custom Cable Assemblies
Custom cable assemblies are designed and manufactured to meet specific requirements, offering unique configurations, lengths, connectors, and materials. Unlike standard off-the-shelf solutions, custom assemblies are tailored to fit precise specifications, ensuring optimal performance and reliability in their intended applications.
Key Considerations for Custom Cable Assemblies
- Design Requirements: The first step in creating a custom cable assembly is understanding the design requirements. This includes the electrical and mechanical properties needed for the application, such as voltage, current, signal integrity, and physical dimensions. Detailed design specifications help manufacturers create assemblies that precisely match the application’s needs.
- Environmental Conditions: Consider the environmental conditions where the cable assembly will be used. Factors such as temperature, humidity, chemical exposure, and mechanical stress can impact the choice of materials and design. For instance, assemblies used in harsh industrial environments may require rugged insulation and protective coatings.
- Connector Types: Choosing the right connectors is crucial for ensuring reliable connections. Connectors must be compatible with the mating components and suitable for the application’s requirements. Options include standard connectors, such as USB or RJ45, and custom connectors designed for specific interfaces.
- Material Selection: The choice of materials for cables, insulation, and connectors affects the assembly’s performance, durability, and flexibility. Common materials include copper for conductors, PVC or Teflon for insulation, and various metals or plastics for connectors. The right material selection ensures the assembly can withstand the intended operational conditions.
- Electrical Specifications: Understanding the electrical requirements, such as signal transmission, power delivery, and electromagnetic compatibility, is critical. Custom assemblies must be designed to handle the specific electrical characteristics of the application, minimizing signal loss and interference.
- Regulatory Compliance: Custom cable assemblies must comply with relevant industry standards and regulations. This includes certifications for electrical safety, environmental compliance (e.g., RoHS), and industry-specific standards (e.g., ISO, UL). Ensuring compliance helps avoid legal issues and ensures the assembly’s reliability and safety.
- Testing and Quality Assurance: Rigorous testing and quality assurance processes are essential for custom cable assemblies. This includes electrical testing, mechanical testing, and environmental testing to verify that the assembly meets all specifications and performs reliably under various conditions. Partnering with cable assemblies manufacturers that prioritize quality assurance is crucial.
- Cost and Lead Time: Budget and lead time considerations are important for custom cable projects. Balancing cost with quality and performance ensures that the final product meets budgetary constraints without compromising on reliability. Clear communication with manufacturers about lead times helps manage project timelines effectively.
Applications of Custom Cable Assemblies
Custom cable assemblies are used in a wide range of industries and applications, including:
- Automotive: Custom assemblies are used in vehicles for power distribution, signal transmission, and connectivity in critical systems like engine controls, infotainment, and safety features.
- Medical Devices: In the medical field, custom cable assemblies ensure reliable connections in diagnostic equipment, patient monitoring systems, and surgical instruments.
- Industrial Automation: Industrial machinery and automation systems rely on custom cable assemblies for efficient operation, ensuring seamless communication between different components and systems.
- Telecommunications: Custom assemblies support the transmission of voice, data, and video signals in telecommunications infrastructure, including base stations, routers, and switches.
- Consumer Electronics: From smartphones to home appliances, custom cable assemblies provide reliable connections for power, data transfer, and signal transmission, enabling the smooth operation of electronic devices.
Conclusion
Choosing the proper components for custom cable assemblies involves careful consideration of design requirements, environmental conditions, material selection, and regulatory compliance. Partnering with reputable cable assembly manufacturers ensures access to high-quality components that meet specific needs, contributing to the reliability and performance of electronic systems. As technology continues to advance, the role of custom cable assemblies will only become more critical in driving innovation and connectivity in various industries.
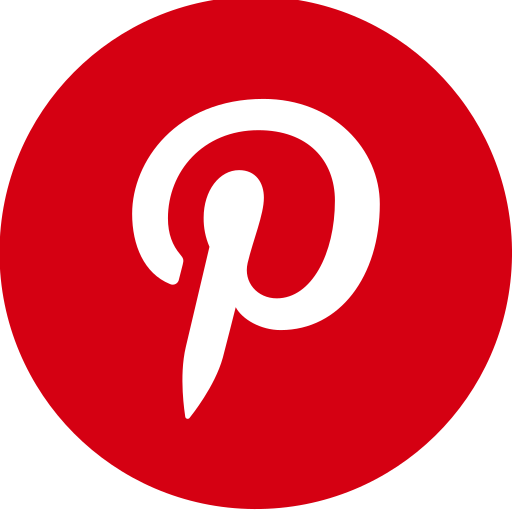