A grinding machine is a powerful tool that is used to grind surfaces and materials to achieve precise dimensions and finishes. The lifespan of a grinding machine can vary significantly depending on several factors, including the type of machine, the frequency and intensity of use, and how well it is maintained. When discussing grinding machines, it is essential to consider the expertise of universal cutter grinder machine manufacturers in India, as they play a crucial role in determining the durability and efficiency of these machines.
Types of Grinding Machines
There are various types of grinding machines, each serving a specific purpose and having a different expected lifespan:
- Surface Grinders: These machines are used to create smooth, flat surfaces. They are commonly found in machine shops and have a moderate lifespan, typically ranging from 10 to 20 years, depending on use and maintenance.
- Cylindrical Grinders: These are used for shaping the outside of an object. They have a similar lifespan to surface grinders but can last longer if used correctly and maintained regularly.
- Tool and Cutter Grinders: These machines sharpen tool bits and cutting tools. They are critical in the manufacturing industry and can last up to 20 years with proper care.
- Bench Grinders: Smaller and less expensive, bench grinders are often used for sharpening tools and other light grinding tasks. Their lifespan is shorter, generally between 5 to 10 years, due to their limited industrial use.
- Belt Grinders: Known for their versatility, these grinders are used for finishing, deburring, and stock removal. With proper maintenance, their lifespan can extend to 15 years or more.
Factors Influencing Lifespan
The lifespan of a grinding machine is influenced by several key factors:
- Quality of Manufacture: Machines built by reputable manufacturers, especially those specializing in universal cutter grinders in India, are designed to last longer and withstand rigorous use.
- Maintenance: Regular maintenance, including cleaning, lubrication, and part replacement, is crucial for extending the life of a grinding machine. Neglect can lead to early wear and tear.
- Frequency of Use: Machines that are used continuously in high-volume production environments will have a shorter lifespan compared to those used less frequently.
- Operating Environment: The conditions in which a machine operates, such as exposure to dust, temperature variations, and humidity, can significantly impact its longevity.
- Operator Skill: Skilled operators who use the machine correctly and avoid overloading it can extend its lifespan considerably.
Maintenance Practices
Effective maintenance practices are vital for ensuring the longevity of a grinding machine. Here are some best practices:
- Regular Inspection: Periodic inspections help identify potential issues before they become severe problems. Checking for wear and tear, alignment issues, and lubrication needs is essential.
- Lubrication: Keeping moving parts well-lubricated reduces friction and wear, extending the life of the machine.
- Cleanliness: Keeping the machine clean, especially in dust-prone environments, prevents contamination and abrasive wear.
- Part Replacement: Timely replacement of worn-out parts, such as grinding wheels, belts, and bearings, prevents further damage to the machine.
- Operator Training: Ensuring that operators are well-trained in using and maintaining the machine helps prevent misuse and extends its lifespan.
Lifespan of Specific Components
Different components of a grinding machine have varying lifespans:
- Grinding Wheels: Typically, grinding wheels need to be replaced after 6 to 12 months of use, depending on the frequency and intensity of grinding tasks.
- Bearings: High-quality bearings can last several years, but they should be inspected regularly and replaced at the first sign of wear.
- Belts and Pulleys: These parts can last up to 5 years, but their lifespan depends on the load and maintenance.
- Spindles: The spindle is a critical component, and its lifespan can range from 5 to 10 years, based on usage and care.
Case Studies
Examining the lifespan of grinding machines in different industrial settings provides valuable insights:
- Automotive Industry: In this sector, grinding machines are heavily used for precision machining of engine components. With rigorous maintenance schedules, these machines can last up to 15 years.
- Tool Manufacturing: Companies producing cutting tools and drills rely on tool and cutter grinders. High-quality machines from reputable universal cutter grinder machine manufacturers in India have been known to last over 20 years with consistent upkeep.
- Metal Fabrication: In metalworking shops, surface and cylindrical grinders are essential. Their lifespan typically ranges from 10 to 15 years, contingent on the workload and maintenance.
Innovations and Future Trends
Technological advancements and innovations are continually enhancing the durability and efficiency of grinding machines. Some notable trends include:
- Automated Maintenance Systems: Integrating sensors and IoT technology enables real-time monitoring of machine conditions, predicting maintenance needs, and preventing unexpected breakdowns.
- Advanced Materials: The use of advanced materials in manufacturing critical components, such as ceramic bearings and high-strength alloys, improves durability.
- Energy Efficiency: Newer models are designed to be more energy-efficient, reducing operational costs and extending the life of the machine by minimizing wear and tear.
- Smart Controls: Modern grinding machines are equipped with smart controls and software that optimize performance and reduce operator error.
Conclusion
The lifespan of a grinding machine is a complex interplay of various factors, including the quality of manufacture, maintenance practices, and the operating environment. By understanding these factors and implementing best maintenance practices, the lifespan of a grinding machine can be significantly extended, ensuring optimal performance and return on investment. Universal cutter grinder machine manufacturers in India, with their expertise and technological advancements, play a crucial role in providing durable and efficient machines that meet the evolving needs of the industry.
Regular maintenance, skilled operation, and staying abreast of technological innovations are key to maximizing the lifespan of grinding machines, making them indispensable assets in various industrial sectors.
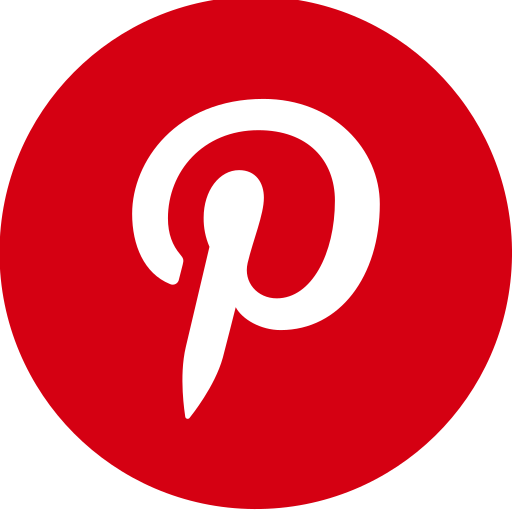