India’s infrastructure sector is booming, and with it, the demand for reliable and efficient cranes and hoists. To keep pace with this growth, hoist crane manufacturers in India are embracing cutting-edge technologies that are revolutionizing the industry. These advancements are not just improving efficiency and safety, but also opening doors to new possibilities in material handling.
Here’s a look at the top 5 technological advancements that are powering innovation in crane and hoist manufacturing in India:
Smarter Cranes with Integrated Control Systems:
Gone are the days of purely mechanical crane operation. Today’s cranes are increasingly equipped with sophisticated control systems that use microprocessors and sensors to automate operations and enhance safety. These systems offer several benefits:
Improved Precision:
Electronic controls allow for more precise movement of the crane, minimizing the risk of load sway and improving overall accuracy during lifting operations.
Enhanced Safety Features:
Integrated overload protection systems prevent exceeding the crane’s lifting capacity, while anti-collision sensors can detect obstacles and automatically stop the crane to avoid accidents.
Real-time Data Monitoring:
Advanced control systems provide real-time data on factors like load weight, crane position, and operating conditions. This allows operators to make informed decisions and identify potential issues before they escalate.
According to a report by Zion Market Research, the global market for industrial control systems in cranes and hoists is expected to reach a staggering USD 4.2 billion by 2025. This growth is a testament to the increasing demand for smarter and safer crane operations in India and around the world.
The Rise of Telematics and Remote Crane Operation:
Telematics, the integration of telecommunication and informatics, is transforming the way cranes are operated. With telematics systems, crane data can be transmitted wirelessly to a remote location, allowing for:
Remote Monitoring and Diagnostics:
Crane managers can monitor crane performance and identify potential maintenance needs remotely, optimizing maintenance schedules and reducing downtime.
Real-time Support:
Service technicians can access crane data remotely and provide real-time troubleshooting assistance to operators on the ground, minimizing downtime and improving efficiency.
Enhanced Safety through Remote Operation:
In hazardous environments, telematics can enable remote crane operation, keeping operators out of harm’s way.
A study by MarketsandMarkets predicts that the global market for telematics in the construction equipment industry will reach USD 10.2 billion by 2023. This highlights the growing adoption of remote crane operation solutions in India’s construction sector.
The Power of 3D Modeling and Simulation for Enhanced Design and Planning:
Three-dimensional (3D) modeling software is revolutionizing the design and planning of crane operations. With 3D models, engineers can create virtual representations of the worksite, including the crane, load, and surrounding structures. This allows for:
Collision Detection and Mitigation:
3D simulations can identify potential collisions between the crane, load, and surrounding obstacles before they occur on the actual site, improving safety and reducing rework.
Enhanced Lift Planning:
Simulations help optimize lift paths and ensure the crane has the capacity to handle the specific load, minimizing risks and maximizing efficiency.
Improved Training and Familiarization:
3D models can be used to create realistic training simulations for crane operators, allowing them to practice procedures in a safe and controlled environment.
The Indian government’s push for digitalization in infrastructure projects is expected to accelerate the adoption of 3D modeling and simulation technologies in crane operations.
Harnessing the Potential of the Internet of Things (IoT) for Connected Cranes:
The Internet of Things (IoT) refers to the interconnection of physical devices with the internet, allowing them to collect and share data. In the context of crane manufacturing, IoT sensors can be embedded in various parts of the crane to collect data on:
Machine health:
Sensor data can provide insights into the health of the crane’s components, allowing for predictive maintenance and preventing unexpected breakdowns.
Environmental conditions:
Real-time data on wind speed, temperature, and humidity can be used to adjust crane operation parameters and ensure safety.
Usage patterns:
Data on crane usage can be used to optimize maintenance schedules and improve overall fleet management.
A report by Frost & Sullivan suggests that the Asia-Pacific region will witness the fastest adoption of IoT in the construction sector, with a projected market size of USD 128.3 billion by 2025. This rapid growth indicates the immense potential of IoT for hoist crane manufacturers in India.
Embracing Sustainable Practices with Eco-Friendly Crane Design:
As environmental consciousness takes center stage, hoist crane manufacturers in India are increasingly focusing on sustainable practices. This includes:
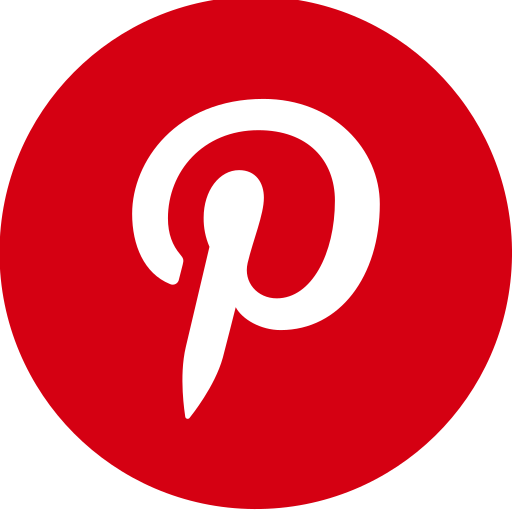