Forged flanges play an important role in a variety of sectors, including oil and gas, petrochemicals, and power production. Forged flanges stand out among the other varieties because of their exceptional strength, resilience to harsh environments, and longevity. As a reliable forged flange manufacturer, BFN recognizes the need to create high-quality flanges that fulfill these industries’ strict criteria. In this article, we will look at the manufacturing process for forged flanges, outlining the essential stages involved in making these crucial components.
Selection of Raw Materials
The first and the most critical operation for the forging of flanges is the selection of high-grade raw materials. Carbon steel, stainless steel, and steel alloys form the common materials for the forging manufacturing of flanges. Selection is also subject to the demands the application places upon the flange by temperature tolerance, the capacity for handling pressure, and corrosion tolerance. BFN Flanges, a trusted forged flanges manufacturer and blind flange supplier ensures high quality raw materials to guarantee the strength and durability for all of our flanges, whether you require blind, slip-on, or weld neck flanges.
Workpiece Cutting
Shearing or sawing techniques are then used to cut the chosen material into billets or blanks. These workpieces’ sizes are determined by taking into consideration machining allowances and material shrinkage, as well as the necessary dimensions of the completed flange.
Heating
A furnace is used to heat the blanks to a precise temperature that makes them both robust and malleable. This temperature varies depending on the material, however, for steel, it normally ranges between 1,150 and 1,250 degrees Celsius (2,100 and 2,300 degrees Fahrenheit).
Forging
After that, the hot workpiece is forged to resemble the flange in shape. The size and dimensions of the flange will determine whether ring rolling, press forging, or hammer forging is used. Forging is done in phases to achieve consistent deformation and improve the grain structure of the metal, hence improving its mechanical qualities.
Post-Forging Heat Treatment
Heat treatment is given to the flanges for the improvement of their mechanical properties after forging. This can comprise quenching, tempering, normalizing, or annealing, subject to the desired qualities. All the flange’s durability, strength, and its capacity for endurance against wear and stress improve through heat treatment. The flange is heat treated after forging for the desired mechanical qualities like less internal stress and enhanced durability. Depending upon the type of material and the desired qualities for the final product, normalizing, annealing, or quenching and tempering is adopted.
Surface finishing and machining
Following heat treatment and forging processes, the flanges are precisely machined for the desired bolt-hole alignments, surface finish, and dimensions. To make the flanges conform to high levels of industry specifications, the flanges are turned, drilled, and faced by the latest computer numeric control machines. Proper bolt holes for the flange are attained through the process of drilling, and the turning is accountable for the shaping of the flange into the desired dimensions.
Inspection and Testing
All the blind flange supplier & forged flanges manufacturer rely on inspection and testing process to ensure the final product is up to the mark. For the purpose of finding defects or irregularities, destructive and non-destructive tests are carried out, including the execution of hydrostatic pressure tests, radiographic inspection, and ultrasonic inspection. This includes the inspection of the flange for defects or irregularities such as surface roughness, porosity, or the presence of cracks. Testing the capability of the flanges for high-pressure and high-temperature applications is one vital measure for their reliability and durability.
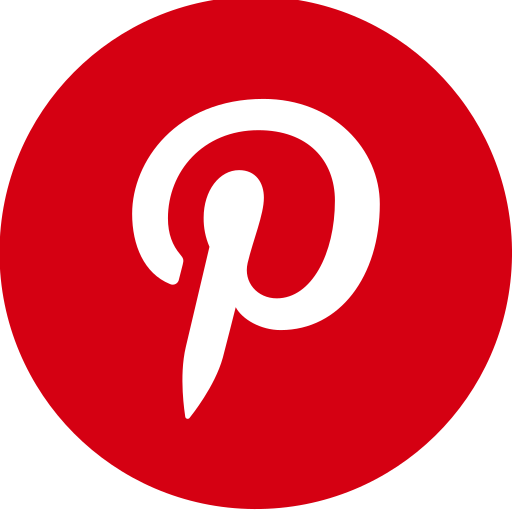