Manufacturing industries are constantly seeking ways to improve efficiency, reduce downtime, and optimize asset performance. One of the most revolutionary advancements in this sector is predictive maintenance, which leverages IoT Gateway Solutions to monitor equipment health and prevent failures before they occur.
IoT Gateway Solutions play a critical role in enabling predictive maintenance by collecting, processing, and transmitting real-time data from machines to analytical platforms. These gateways ensure seamless communication between sensors, edge devices, and cloud-based systems, making predictive maintenance a reality for manufacturers.
- Predictive maintenance can reduce downtime by up to 50%.
- IoT-driven maintenance reduces overall maintenance costs by 25-30%.
- The global predictive maintenance market is expected to reach $23.5 billion by 2026.
Understanding Predictive Maintenance in Manufacturing
What is Predictive Maintenance?
Predictive maintenance (PdM) is a data-driven approach that uses advanced analytics, machine learning, and IoT technology to monitor equipment conditions and predict failures before they occur. Unlike reactive maintenance (fixing a machine after failure) or preventive maintenance (scheduled servicing), PdM ensures that maintenance is performed only when necessary, reducing unnecessary downtime and repair costs.
Key Benefits of Predictive Maintenance
- Reduces Unplanned Downtime: By predicting failures before they occur, manufacturers can plan maintenance proactively.
- Lowers Maintenance Costs: Avoids unnecessary servicing and reduces emergency repair expenses.
- Enhances Equipment Lifespan: Regular monitoring prevents excessive wear and tear.
- Optimizes Workforce Efficiency: Reduces the need for manual inspections and allows workers to focus on more critical tasks.
Role of IoT in Predictive Maintenance
The Importance of IoT in Modern Manufacturing
The integration of IoT in manufacturing has revolutionized the industry by providing real-time insights, automating processes, and optimizing operations. IoT-driven predictive maintenance is a prime example of how connectivity and smart technology can prevent machine failures and maximize efficiency.
Key Technologies Powering IoT Predictive Maintenance
- IoT Sensors: Collect real-time data on temperature, vibration, pressure, and other machine conditions.
- Edge Computing: Processes data at the edge to reduce latency and enable real-time decision-making.
- Cloud Analytics: Stores and analyzes large volumes of data for deeper insights.
- Machine Learning Models: Identify patterns and predict failures based on historical data.
IoT Gateway Solutions: The Backbone of Predictive Maintenance
What are IoT Gateway Solutions?
IoT Gateway Solutions act as intermediaries between IoT devices and cloud systems. They collect, process, and transmit data from sensors to analytical platforms, ensuring seamless communication and efficient predictive maintenance.
How IoT Gateway Solutions Enable Predictive Maintenance
- Data Collection: IoT gateways collect data from multiple sensors installed on manufacturing equipment.
- Edge Processing: Perform real-time analytics to detect anomalies before transmitting data to the cloud.
- Secure Communication: Encrypts data to prevent cyber threats and unauthorized access.
- Cloud Integration: Sends critical insights to cloud-based AI models for advanced analytics.
Key Components of IoT Gateway Solutions in Manufacturing
- Sensor Interface: Connects with IoT sensors to collect data.
- Communication Module: Supports multiple protocols (Wi-Fi, Bluetooth, Zigbee, LoRaWAN).
- Edge Computing Processor: Processes data locally before transmitting to the cloud.
- Security Layer: Ensures encrypted and secure data transmission.
Data Acquisition and Processing in IoT Gateway Solutions
How IoT Gateways Collect and Transmit Data
IoT gateways manage the flow of data from sensors to cloud-based AI/ML models, enabling accurate predictive maintenance.
- Sensors Collect Data: IoT sensors monitor machine health metrics like temperature, vibration, and energy consumption.
- Edge Processing: Raw data is cleaned, filtered, and aggregated at the gateway to remove noise and improve efficiency.
- Secure Transmission: Processed data is encrypted and sent via secure protocols (MQTT, CoAP, HTTP, OPC-UA) to cloud or on-premises servers.
- AI/ML Analysis: Machine learning models analyze the data to detect anomalies, predict failures, and generate maintenance alerts.
Edge Computing and Real-Time Analytics
One of the biggest advantages of IoT Gateway Solutions is their ability to process data locally at the edge before sending it to cloud servers.
- Reduces Cloud Dependency: Instead of sending raw data directly to the cloud, IoT gateways filter and analyze it locally, reducing bandwidth usage and cloud storage costs.
- Lowers Latency: By processing data in real-time, IoT gateways enable instant decision-making, ensuring that maintenance teams can respond to potential failures without delays.
- Enhances Security: Keeping sensitive data within the local network reduces the risk of cyberattacks compared to transmitting unprocessed data to remote servers.
- Improves Operational Efficiency: Real-time analytics at the edge ensures that only actionable and relevant data is transmitted, reducing network congestion and improving response times.
Communication Protocols in IoT Gateway Solutions
IoT Gateway Solutions rely on various communication protocols to securely and efficiently transmit data between sensors, edge devices, and cloud platforms. These protocols ensure reliable, low-latency, and energy-efficient data exchange, which is crucial for predictive maintenance in manufacturing.
- MQTT (Message Queuing Telemetry Transport): A lightweight, publish-subscribe protocol designed for low-bandwidth and high-latency environments, making it ideal for industrial IoT applications.
- CoAP (Constrained Application Protocol): A compact protocol optimized for resource-constrained devices with limited processing power and memory, ensuring efficient communication in IoT networks.
- HTTP (HyperText Transfer Protocol): A widely used protocol that enables seamless integration with web-based applications and cloud platforms, supporting real-time monitoring and control.
Security Challenges in IoT Gateway Solutions for Predictive Maintenance
Ensuring security in IoT Gateway Solutions is crucial for maintaining the integrity, confidentiality, and availability of predictive maintenance data. These gateways handle sensitive machine health data and are vulnerable to cyber threats that could disrupt manufacturing operations.
Common Threats and Vulnerabilities
- Unauthorized Access to IoT Devices: Hackers can exploit weak authentication mechanisms to gain control over IoT gateways and disrupt operations.
- Data Breaches and Cyberattacks: Unsecured data transmission can lead to data leaks, compromising predictive maintenance insights.
- Network Vulnerabilities in Wireless Communication: Weak encryption and insecure protocols can expose IoT networks to man-in-the-middle (MITM) attacks, denial-of-service (DoS) attacks, and malware intrusions.
Best Practices for Securing IoT Gateways
- Use End-to-End Encryption: Encrypt data using TLS/SSL protocols to ensure secure communication between sensors, gateways, and cloud platforms.
- Implement Multi-Factor Authentication (MFA): Restrict unauthorized access by requiring multiple authentication factors for device and network entry.
- Regularly Update Firmware: Apply security patches and updates to prevent exploits targeting outdated software and IoT gateway vulnerabilities.
Real-World Applications of IoT Gateway Solutions in Manufacturing
IoT Gateway Solutions play a crucial role in predictive maintenance across various manufacturing sectors. By enabling real-time monitoring, anomaly detection, and proactive maintenance, these solutions help industries reduce downtime, optimize operations, and extend equipment lifespan.
Automotive Industry
- Predicts failures in assembly line robots by continuously monitoring motor temperature, vibration levels, and operational efficiency.
- Prevents unexpected breakdowns, ensuring uninterrupted production and higher efficiency.
Food Processing Units
- Monitors refrigeration units to maintain optimal temperature and humidity levels, preventing food spoilage.
- Detects early signs of compressor or cooling system failures, ensuring compliance with food safety regulations.
Heavy Machinery Manufacturing
- Detects anomalies in hydraulic and pneumatic systems by analyzing pressure, fluid levels, and component wear.
- Helps prevent costly repairs and unplanned downtime, extending machine lifespan and improving operational efficiency.
Conclusion
IoT Gateway Solutions are transforming predictive maintenance in manufacturing by enabling real-time monitoring, advanced analytics, and seamless data transmission. With proper security measures, robust communication protocols, and AI-driven insights, manufacturers can minimize downtime, reduce costs, and enhance efficiency.
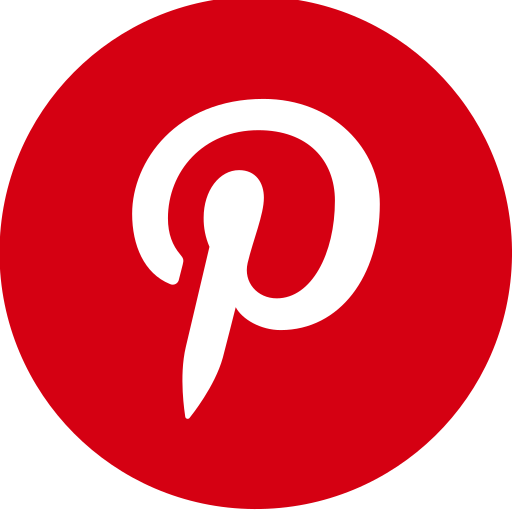