Embroidery has long been celebrated as an art form that combines creativity with craftsmanship. From intricate logos on corporate uniforms to personalized designs on gifts, the quality of embroidery can make or break the final product. At the heart of this process lies embroidery digitizing—the transformation of artwork into a digital file that instructs machines on how to stitch. Modern digitizing services have elevated this craft, ensuring designs are not only visually stunning but also technically flawless. This blog explores how digitizing services enhance design quality, their key techniques, and their impact on the embroidery industry.
Understanding Embroidery Digitizing
Embroidery digitizing is the bridge between a designer’s vision and the finished embroidered piece. It involves converting an image, logo, or pattern into a stitch file that an embroidery machine can read. This file dictates stitch types (satin, fill, or running), directions, densities, and sequences. While the process was once manual—relying on skilled digitizers to painstakingly map every detail—today’s advanced digitizing services use technology and expertise to deliver superior results. The outcome? Designs that are sharper, more durable, and true to the original artwork.
Why Design Quality Matters in Embroidery
In embroidery, quality isn’t just about aesthetics; it’s about functionality and longevity. A poorly digitized design can lead to uneven stitches, thread breaks, fabric puckering, or faded details over time. Whether it’s a brand logo on a jacket or a decorative pattern on a quilt, high-quality digitizing ensures the design stands out and withstands wear. Digitizing services play a crucial role in achieving this balance, blending precision with creativity to elevate the final product.
How Digitizing Services Enhance Design Quality
1. Precision in Stitch Mapping
Digitizing services excel at translating complex designs into precise stitch patterns. By carefully determining stitch angles and lengths, they ensure every curve, line, and detail is accurately represented. For example, a logo with fine text or intricate gradients requires meticulous stitch placement—something professional digitizing achieves effortlessly, resulting in crisp, professional outcomes.
2. Optimal Stitch Density
Too many stitches can make a design bulky and stiff; too few can leave it sparse and underwhelming. Digitizing services strike the perfect balance by adjusting stitch density based on the design and fabric. This enhances visual clarity while preventing issues like thread buildup or fabric distortion, ensuring the embroidery feels as good as it looks.
3. Fabric-Specific Adjustments
Not all fabrics are created equal. A design that works on cotton may fail on satin or denim without proper adjustments. Digitizing services analyze the target material—its thickness, stretch, and texture—and tweak the stitch file accordingly. This customization minimizes puckering, ensures smooth stitching, and enhances durability, making the design pop on any surface.
4. Color Matching and Layering
Embroidery often involves multiple thread colors, and poor digitizing can lead to misaligned layers or clashing hues. Professional services use advanced software to map color transitions and layer stitches seamlessly. This attention to detail preserves the design’s vibrancy and depth, creating a polished, cohesive look.
5. Error Prevention
Human error can plague manual digitizing—think skipped stitches, overlapping threads, or unbalanced tension. Digitizing services leverage technology to spot and correct these issues before stitching begins. By simulating the design virtually, they eliminate guesswork, ensuring the machine executes it flawlessly.
6. Consistency Across Multiple Pieces
For businesses producing bulk orders—like branded apparel or promotional items—consistency is key. Digitizing services create standardized files that guarantee every piece, from the first to the hundredth, looks identical. This uniformity strengthens brand identity and customer satisfaction.
The Role of Technology in Digitizing Services
Modern digitizing services owe much of their success to technology. Software like Wilcom, Pulse, and Hatch allows digitizers to fine-tune designs with unparalleled accuracy. Some even integrate artificial intelligence (AI) to automate stitch mapping, predict fabric behavior, and suggest improvements. This tech-driven approach doesn’t replace human expertise but enhances it, enabling digitizers to focus on creative refinements while the software handles technical precision.
Real-World Benefits of Quality Digitizing
The impact of professional digitizing services is evident across industries. Fashion designers use them to bring intricate patterns to life on delicate fabrics, ensuring every stitch aligns with their vision. Small businesses rely on digitizing to produce consistent logos on merchandise, boosting their professional image. Even hobbyists benefit, turning simple sketches into detailed embroidered gifts with ease. The result is a versatile service that caters to diverse needs while upholding high standards.
Comparing Manual vs. Professional Digitizing
Manual digitizing, while artisanal, is time-consuming and prone to inconsistencies. A skilled digitizer might spend hours on a single design, only for minor errors to emerge during stitching. Professional embroidery digitizing services, on the other hand, combine human oversight with advanced tools to deliver faster, more reliable results. This hybrid approach ensures creativity isn’t sacrificed for efficiency, offering the best of both worlds.
Challenges in Achieving High-Quality Digitizing
Despite their advantages, digitizing services face challenges. Complex designs with fine details or gradients can test even the best software, requiring manual tweaks. Additionally, inexperienced providers may overlook fabric compatibility, leading to subpar results. Clients must choose reputable services with a track record of excellence to avoid these pitfalls.
The Future of Digitizing Services
The future of embroidery digitizing is bright, with innovations on the horizon. AI and machine learning could further streamline the process, predicting optimal stitch patterns with minimal input. Augmented reality (AR) might allow designers to preview digitized designs on fabric in real time, refining them before stitching. As embroidery machines evolve, digitizing services will adapt, ensuring quality keeps pace with technology.
Conclusion
Digitizing services for embroidery are more than a technical step—they’re a cornerstone of design quality. By enhancing precision, adapting to fabrics, and leveraging technology, they transform ideas into stunning, durable embroidered pieces. Whether you’re a business owner, designer, or enthusiast, these services elevate your work, ensuring every stitch tells a story of excellence. As the industry continues to innovate, digitizing will remain at the forefront, stitching quality into the fabric of embroidery’s future.
FAQs: How Digitizing Services for Embroidery Improve Design Quality
1. What is embroidery digitizing?
Embroidery digitizing is the process of converting artwork into a digital stitch file that embroidery machines use to create designs on fabric.
2. How do digitizing services improve design quality?
They enhance precision, optimize stitch density, adjust for fabrics, and prevent errors, resulting in clearer, more durable embroidery.
3. Can I digitize a design myself?
Yes, with basic software and skills, but professional services offer superior quality, especially for complex or bulk designs.
4. Why is stitch density important?
Proper stitch density ensures the design looks full without being overly heavy, maintaining both aesthetics and fabric integrity.
5. Do digitizing services work for all fabrics?
Yes, reputable services adjust stitch settings for different materials, from cotton to leather, ensuring consistent quality.
6. How long does digitizing take?
It depends on complexity, but professional services can digitize a design in hours, compared to days for manual methods.
7. Are digitizing services expensive?
Costs vary, but they’re often affordable, especially considering the time saved and quality gained. Prices typically range from $10-$50 per design.
8. Can digitizing fix a bad design?
It can enhance execution, but the original artwork’s clarity and detail heavily influence the final embroidered quality.
9. What’s the difference between manual and professional digitizing?
Manual digitizing is slower and less consistent, while professional services use technology and expertise for faster, precise results.
10. How do I choose a good digitizing service?
Look for providers with positive reviews, experience with similar projects, and samples showcasing high-quality, detailed work.
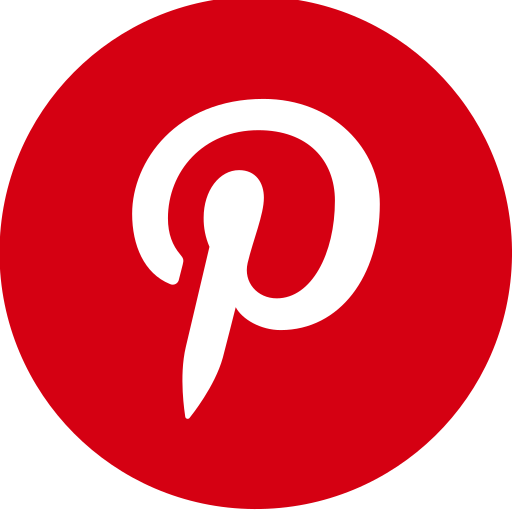