Telescopic covers are vital components in the manufacturing industry, particularly in protecting machinery and ensuring smooth operations. They are designed to safeguard machine tools from debris, coolants, and other contaminants, thereby extending the life of the equipment and maintaining its precision.
The Importance of Telescopic Covers
Protection and Maintenance
Telescopic covers provide robust protection for the delicate parts of machinery. They are engineered to withstand harsh industrial environments, preventing metal shavings, dust, and other particles from damaging the machinery. This protection is crucial in maintaining the efficiency and longevity of the equipment.
Enhancing Machine Performance
By shielding the machine components, telescopic covers help in maintaining the precision of the equipment. This precision is essential in industries where accuracy is paramount, such as aerospace, automotive, and electronics manufacturing. The covers also facilitate smoother operation, reducing downtime and maintenance costs.
Types of Telescopic Covers
Steel Telescopic Covers
Steel telescopic covers are known for their durability and strength. They are ideal for applications involving heavy-duty machinery where maximum protection is required. These covers are often used in environments where there is a high risk of impact and abrasion.
Stainless Steel Telescopic Covers
Stainless steel telescopic covers offer corrosion resistance and are suitable for environments where exposure to moisture and chemicals is common. They are widely used in the food processing, pharmaceutical, and chemical industries.
Aluminum Telescopic Covers
Aluminum telescopic covers are lightweight and resistant to corrosion. They are often used in applications where weight is a critical factor. These covers are suitable for industries such as electronics and precision engineering.
Manufacturing Process of Telescopic Covers
The manufacturing process of telescopic covers involves several stages, including design, material selection, cutting, forming, welding, and finishing. Advanced technologies and machinery are used to ensure precision and quality in every step.
Design and Material Selection
The design of telescopic covers is customized based on the specific requirements of the machinery they will protect. Material selection is crucial, as it determines the durability and performance of the covers. Common materials include steel, stainless steel, and aluminum.
Cutting and Forming
Cutting and forming are essential steps in the manufacturing process. Precision cutting tools and forming machines are used to shape the materials into the desired dimensions and configurations. This stage requires meticulous attention to detail to ensure the accuracy of the final product.
Welding and Assembly
Welding is a critical step in assembling the telescopic covers. It ensures that the components are securely joined together, providing structural integrity and strength. Advanced welding techniques are employed to achieve high-quality welds that can withstand the demanding industrial environment.
Finishing and Quality Control
The finishing process involves surface treatment to enhance the durability and appearance of the covers. This may include painting, coating, or polishing. Quality control measures are implemented throughout the manufacturing process to ensure that the covers meet the highest standards of quality and performance.
Bellows Covers Manufacturers
Introduction
Bellows covers are essential protective devices used in various industrial applications. They are designed to shield machine components from dust, debris, and other contaminants, ensuring the smooth and efficient operation of the machinery.
Types of Bellows Covers
Round Bellows
Round bellows are commonly used to protect cylindrical components such as shafts and screws. They are flexible and can accommodate a wide range of motion, making them ideal for dynamic applications.
Rectangular Bellows
Rectangular bellows are used to protect flat surfaces and linear motion systems. They are often found in applications such as guideways, machine beds, and lifting tables.
Folded Bellows
Folded bellows are designed for applications requiring compact and efficient protection. They can be customized to fit various shapes and sizes, providing versatile protection for different machine components.
Manufacturing Process of Bellows Covers
The manufacturing process of bellows covers involves several steps, including design, material selection, cutting, forming, and finishing. Advanced techniques and machinery are used to ensure precision and quality in every stage.
Design and Material Selection
The design of bellows covers is tailored to the specific requirements of the machinery they will protect. Material selection is crucial, as it determines the flexibility, durability, and resistance of the covers. Common materials include fabric, rubber, and plastic.
Cutting and Forming
Precision cutting tools and forming machines are used to shape the materials into the desired dimensions and configurations. This stage requires meticulous attention to detail to ensure the accuracy and quality of the final product.
Assembly and Finishing
The assembly process involves joining the components of the bellows covers using various techniques such as sewing, welding, or gluing. The finishing process may include treatments to enhance the durability and appearance of the covers.
Laser Machine Bellows Manufacturers
Introduction
Laser machine bellows are specialized protective covers designed to shield laser cutting and engraving machines from dust, debris, and other contaminants. They are crucial in maintaining the precision and efficiency of laser machines.
Types of Laser Machine Bellows
Accordion Bellows
Accordion bellows are commonly used in laser machines due to their flexibility and compact design. They can expand and contract easily, providing effective protection for the machine components.
Seamless Bellows
Seamless bellows are designed for applications requiring a high level of precision and cleanliness. They are made from materials that can withstand the intense heat and radiation produced by laser machines.
Manufacturing Process of Laser Machine Bellows
The manufacturing process of laser machine bellows involves several stages, including design, material selection, cutting, forming, and finishing. Advanced technologies and machinery are used to ensure precision and quality in every step.
Design and Material Selection
The design of laser machine bellows is customized based on the specific requirements of the laser machines they will protect. Material selection is crucial, as it determines the flexibility, durability, and resistance of the covers. Common materials include fabric, rubber, and plastic.
Cutting and Forming
Precision cutting tools and forming machines are used to shape the materials into the desired dimensions and configurations. This stage requires meticulous attention to detail to ensure the accuracy and quality of the final product.
Assembly and Finishing
The assembly process involves joining the components of the bellows covers using various techniques such as sewing, welding, or gluing. The finishing process may include treatments to enhance the durability and appearance of the covers.
Conclusion
Telescopic covers, bellows covers, and laser machine bellows are essential components in the scutesbellows manufacturing industry, providing critical protection for machinery and ensuring smooth operations. Their design, material selection, and manufacturing processes are tailored to meet the specific requirements of the applications they serve. By investing in high-quality protective covers, industries can enhance the performance, efficiency, and longevity of their machinery.
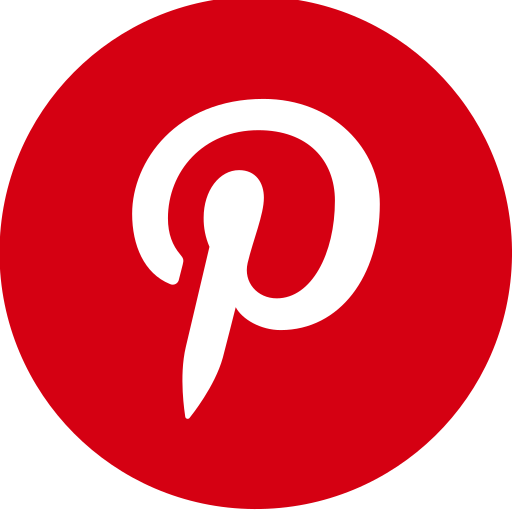