Introduction to HDPE Pipes and Fittings
High-density polyethylene (HDPE) pipes and fittings have revolutionized various industries with their durability, versatility, and eco-friendly benefits. Known for their flexibility and corrosion resistance, HDPE pipes are widely used in water supply systems, industrial applications, and more. In this article, we’ll delve into what makes HDPE pipes and fittings stand out and explore their wide range of uses.
What is HDPE?
HDPE, or High-Density Polyethylene, is a type of plastic renowned for its high strength-to-density ratio. Its unique properties make it a preferred choice for manufacturing pipes and fittings that must withstand extreme environmental conditions.
Overview of HDPE Pipe Applications
HDPE pipes are widely used across various industries, including agriculture, construction, and mining. These pipes are ideal for transporting water, gas, and chemicals due to their flexibility, strength, and low maintenance requirements.
Benefits of Using HDPE Pipes and Fittings
Durability and Longevity
HDPE pipes are incredibly durable, with a life expectancy of 50 to 100 years. Their resistance to cracking and abrasion ensures they withstand tough environmental conditions, which makes them ideal for buried applications.
Resistance to Corrosion and Chemicals
Unlike metal pipes, HDPE pipes do not rust or corrode, making them highly suitable for transporting corrosive materials. Additionally, HDPE’s chemical resistance enables it to handle a variety of industrial fluids and gases.
Flexibility and Cost-Effectiveness
HDPE’s flexibility allows for ease of installation, especially in complex terrains. This feature significantly reduces installation time and costs, making HDPE pipes a cost-effective solution for many projects.
Types of HDPE Pipes
HDPE Pressure Pipes
Designed to handle high pressure, these pipes are widely used in water and gas transportation. They come in various pressure ratings to accommodate different applications.
Non-Pressure HDPE Pipes
Non-pressure HDPE pipes are often used for drainage and wastewater systems. These pipes can be perforated or solid, depending on the specific application needs.
HDPE Corrugated Pipes
These pipes are mainly used for stormwater drainage and culvert installations. The corrugated design adds strength while reducing weight, which is advantageous for installations requiring large-diameter pipes.
Types of HDPE Fittings
Couplers and End Caps
Couplers connect two pipe sections, while end caps are used to close off pipe ends. Both are essential in constructing robust
HDPE piping systems.
Elbows and Bends
Elbows and bends are used to change the direction of HDPE piping systems. Available in various angles, they offer flexibility in system design and installation.
HDPE Flanges and Connectors
Flanges and connectors are used for joining HDPE pipes to different pipe materials or equipment. They offer a secure connection that maintains the system’s integrity under pressure.
HDPE Pipe Manufacturing Process
Raw Materials and Extrusion Process
The production of HDPE pipes involves melting HDPE resin pellets, which are then extruded into a pipe shape. This process is carefully controlled to ensure the pipe meets quality standards.
Quality Control in Manufacturing
Strict quality checks are conducted throughout the manufacturing process to ensure that HDPE pipes meet durability and performance standards.
Installation of HDPE Pipes and Fittings
Equipment Needed for Installation
HDPE pipe installations require specific equipment, such as fusion machines, which weld pipes together. Proper installation techniques are crucial for the integrity and longevity of the piping system.
Step-by-Step Installation Process
The installation process involves trench preparation, pipe fusion, and placement. Each step requires careful planning and execution to avoid issues later on.
Safety Tips During Installation
Safety is paramount when handling HDPE pipes, especially during fusion and trenching. Workers should wear protective gear and follow safety protocols to prevent accidents.
Maintenance and Repair of HDPE Pipes
Preventative Maintenance Tips
Regular inspections and preventative maintenance help prolong the lifespan of HDPE pipes. Monitoring for signs of wear can help avoid costly repairs.
Common Repair Techniques
HDPE pipes are repairable through several methods, including fusion welding and using HDPE repair kits. These techniques are cost-effective and help restore system functionality quickly.
HDPE Pipes vs. Traditional Pipe Materials
HDPE vs. PVC Pipes
HDPE pipes offer superior flexibility and chemical resistance compared to PVC pipes, which makes them a better choice for certain applications.
HDPE vs. Metal Pipes
Unlike metal pipes, HDPE pipes do not rust, which enhances their longevity and reduces maintenance costs over time.
Environmental Impact of HDPE Pipes
Recyclability of HDPE
HDPE is 100% recyclable, which reduces waste and environmental impact. HDPE’s recyclability aligns with sustainable practices, making it a preferred material in eco-conscious projects.
Carbon Footprint Reduction with HDPE
Using HDPE pipes can lower carbon emissions due to their long life expectancy and minimal maintenance needs, which reduces the need for frequent replacements.
Industry Standards and Regulations
Compliance Standards for HDPE Pipes
HDPE pipes must meet specific industry standards, such as ISO and ASTM certifications, which guarantee their quality and safety for various applications.
Certifications for Quality Assurance
Manufacturers often seek certifications to demonstrate that their HDPE pipes meet rigorous quality standards, which provides customers with confidence in the product’s reliability.
Common Applications of HDPE Pipes and Fittings
Plumbing and Drainage
HDPE pipes are ideal for plumbing systems due to their flexibility and durability. They are also used extensively in drainage systems to efficiently handle wastewater.
Agricultural Irrigation Systems
HDPE pipes are widely used in agriculture for irrigation systems. Their resistance to corrosion and chemicals makes them suitable for transporting water and fertilizers.
Industrial and Mining Applications
Industries and mines use HDPE pipes for transporting chemicals, slurry, and wastewater due to their chemical resistance and robustness.
Cost Comparison: HDPE vs. Other Materials
Installation Costs
HDPE pipes have lower installation costs due to their flexibility and lightweight properties, which reduce labor and equipment expenses.
Maintenance and Repair Costs
Compared to other materials, HDPE pipes require less maintenance, translating to lower lifetime costs and fewer repairs.
Tips for Selecting the Right HDPE Pipes and Fittings
Assessing Pipe and Fitting Requirements
It’s crucial to assess project needs, including pressure ratings and environmental factors, before selecting HDPE pipes and fittings.
Evaluating Product Quality and Durability
Selecting high-quality HDPE pipes from reputable manufacturers ensures a reliable and long-lasting piping system.
Troubleshooting Common HDPE Pipe Issues
Identifying Leaks and Cracks
Leaks and cracks can often be identified by a drop in pressure or visible signs on the pipe surface. Prompt repair prevents further issues.
Dealing with Pressure Drops
Pressure drops may indicate blockages or leaks. Routine checks can help identify and resolve these issues before they become major problems.
Future Trends in HDPE Pipes and Fittings
Advancements in HDPE Materials
Innovations in HDPE materials, such as reinforced composites, are enhancing pipe performance, making them even more durable and versatile.
Emerging Applications in New Industries
With advancements in technology, HDPE pipes are finding new applications in fields like renewable energy and environmental engineering.
FAQs about HDPE Pipes and Fittings
What are HDPE pipes commonly used for?
HDPE pipes are used for water supply, drainage, irrigation, and gas transport due to their flexibility, strength, and chemical resistance.
How durable are HDPE pipes?
HDPE pipes typically last 50 to 100 years, depending on the environment and application.
Are HDPE pipes safe for drinking water?
Yes, HDPE pipes are commonly used for potable water and meet safety standards for water transport.
How do you connect HDPE pipes?
HDPE pipes are typically connected through fusion welding, which creates a strong, leak-proof joint.
Can HDPE pipes be recycled?
Yes, HDPE pipes are fully recyclable, making them an environmentally friendly choice.
What is the main difference between HDPE and PVC pipes?
The main difference is that HDPE is more flexible and chemically resistant, making it better suited for various industrial applications.
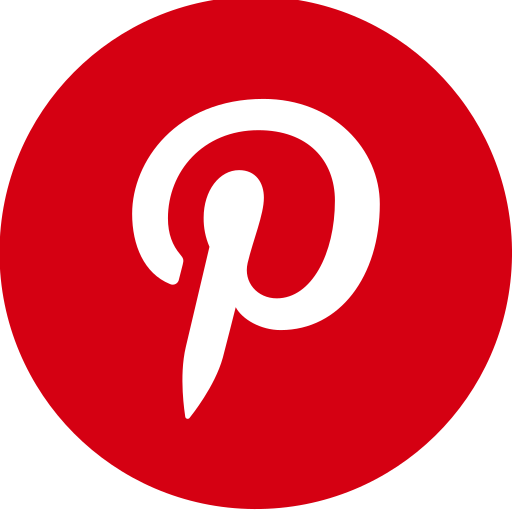