Pad printing is a versatile graphic printing technique used extensively in industry for applying logos, designs, text and other identification markings onto a variety of substrates. As a leading provider of pad printing services in China, Junying offers complete pad printing solutions tailored to clients' die casting and metal component decoration needs. This article will explore the pad printing process, its advantages over alternative printing methods, applications on metal parts and Junying's expertise in delivering high quality pad printed surfaces.
What is Pad Printing?
Pad printing is a form of relief printing where an image is first etched or engraved onto a printing plate, commonly known as the cliché or gravure cylinder. This engraved cylinder is mounted onto a silicone rubber pad which then uses this recessed image to transfer wet ink onto a substrate in a single, rapid impression.
The pad printer machine holds the pad and substrate in place using precisely controlled pneumatic motors. Ink is deposited onto the pad during the flooding stage, then the squeegee blade presses excess ink back leaving ink only in the recessed areas. As the substrate passes under, the exact image from the gravure wells is transferred in perfect register through delicate contact with the silicone pad.
Multiple printing stations with different pads and inks enable complex multi-color designs. Fine details as small as 0.35mm can be achieved on a huge variety of surfaces ranging from flat paper and film to curved glass, ceramic, plastic and metal components. Pad printing maintains sharp image resolution even on irregularly shaped parts through minimal contact pressure.
Pad Printing at Junying
For over a decade, Junying has invested in state-of-the-art pad printing equipment including fully automated semi-rotary and flat bed machines. Their facility houses multiple pad printing lines configured for low to high volume production. Experience with diverse metallic substrates from aluminum, zinc and magnesium alloys aids in perfecting pre-treatment and post-finishing steps.
Junying's pad printing specialists are proficient in design file processing, platemaking, ink development and color matching. Digital artwork files from clients undergo pre-press checking followed by on-site plate production using precision milling machines. A dedicated R&D lab holds comprehensive ink libraries and color standards for accurate replication.
As an integrated manufacturer, Junying provides value-added services beyond graphic decoration. From casting to CNC machining, secondary operations and assembly – all work is handled under one roof with strict quality protocols for batch traceability. This end-to-end control enables just-in-time prototyping and production to compress lead times.
Advantages of Pad Printing
The dominant reasons for pad printing's prevalence are its unique advantages over competing graphic application techniques:
-
Complex Part Compatibility: Pad printing can deposit inks onto three-dimensional and hard-to-reach surfaces with minimal foiling or obstruction.
-
High Resolution: Fine linework and crisp text down to 0.35mm is achievable through silicone pad's conformal contact and applied squeegee pressure.
-
Versatile Color Capability: Up to 8 stations enable vibrant multicolor designs through sequential register printing of CMYK inks.
-
Durability: Properly cured pad printed surfaces demonstrate excellent adhesion, abrasion and chemical resistance rated for years of usage.
-
Economical Scale: Pad printing remains cost-effective for short to medium production volumes ranging from small batches to tens of thousands of units.
-
Minimal Waste: Ink is transferred with very little overspray making it an environmentally sustainable process.
Applications of Pad Printing
Leveraging these strengths, pad printing finds widespread deployment across sectors handling intricate metal components and electronic devices:
-
Consumer Electronics: Mobile devices, cameras, USB drives, small appliances benefit from graphic personalization and identifying marks.
-
Automotive: Ignition parts, gauges, control panels derive protection and visual information from durable pad printed logos and indicators.
-
Medical: Implants, devices, instruments receive identifying traceability codes enabling safety and regulation compliance.
-
Industrial Equipment: Valves, sensors, connectors gain resistance to wear factors like pressure, temperature and chemicals from graphics.
-
Packaging Materials: Cans, bottles, caps show vibrant multi-hue designs on metallic substrates catering to branding needs.
Service Capabilities at Junying
Junying serves as a one-stop solution provider for clients' pad printing requirements:
-
Consultation on design artwork processing, platemaking, inks and colors. Approval sampling for prototypes.
-
Precision surface preparation through multi-stage cleaning and pre-treatment suited for part composition.
-
Automated pad printing using latest flat bed and semi-rotary machines for mass production volumes.
-
Post-printing checks using inspection stations with digital cameras and lights for 100% defect detection.
-
Rigorous quality control tests and certification according to client and industry standards.
-
Packing and logistics management till delivery as per consignments and schedules.
-
Technical support on ink formulations, platemaking solutions, machine operation and maintenance support.
-
On-time manufacturing across entire order cycle from sample runs to large quantity production.
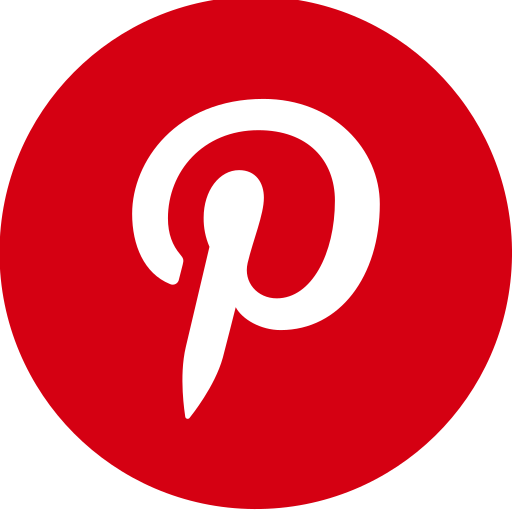