Pneumatic actuators are indispensable components in many industrial systems, providing a simple yet efficient solution for the automation of mechanical movements. These devices convert compressed air energy into mechanical motion, offering industries a reliable way to automate valves, dampers, or other mechanical systems. Their design ensures precision, control, and long-term durability, making them a popular choice across various sectors. In this guide, we will explore the different types of pneumatic actuators, their uses, and their benefits in industrial settings.
What is a Pneumatic Actuator?
A pneumatic actuator is a mechanical device that harnesses the power of compressed air to produce linear or rotary motion. The actuator typically consists of a cylinder and piston mechanism, with compressed air entering the cylinder to move the piston and generate motion. Depending on the design, pneumatic actuators can either push and pull in a linear motion or rotate in circular motion, making them versatile in handling different mechanical tasks.
Pneumatic actuators are used primarily in automation processes and control applications. They are commonly found in industries such as oil and gas, chemical processing, manufacturing, water treatment, and more.
Types of Pneumatic Actuators
Pneumatic actuators come in various designs, each serving a specific purpose. Below are the most common types:
1. Linear Actuators
Linear actuators produce motion in a straight line. They are typically used to open or close valves, move parts in machines, or lift objects in automated systems. There are two main types of linear actuators:
Single-acting Actuators: In this type, compressed air is supplied to one side of the piston, and the return movement relies on a spring or external force.
Double-acting Actuators: Here, compressed air is applied to both sides of the piston, allowing for greater control over both forward and backward movements.
2. Rotary Actuators
Rotary actuators are used when rotational motion is required. These actuators convert compressed air energy into angular displacement or torque. They are commonly used in applications where valves need to be rotated for flow control. Rotary actuators are further divided into:
Rack and Pinion Actuators: A rack and pinion mechanism converts linear motion into rotational motion. This type is commonly used for actuating butterfly and ball valves.
Vane Actuators: Vane actuators use a pivoting vane that moves under air pressure, resulting in angular motion. They are suitable for applications that require limited rotation.
Uses of Pneumatic Actuators
Pneumatic actuators are highly versatile and can be found in many industrial settings. Some of the most common uses include:
1. Valve Automation
In industries such as oil and gas, chemical processing, and water treatment, valves are integral to controlling fluid flow. Pneumatic actuators are frequently used to automate the opening and closing of these valves, allowing for precise control over flow rates, pressure, and system safety.
2. Material Handling
In manufacturing and assembly lines, pneumatic actuators are often employed to lift, push, or pull materials. They can handle repetitive motion tasks, such as moving components in a production line, with high precision and speed.
3. Damper Control
In HVAC (Heating, Ventilation, and Air Conditioning) systems, pneumatic actuators control dampers that regulate airflow. This is crucial for maintaining optimal temperatures and ventilation in industrial buildings.
4. Automated Packaging Systems
Pneumatic actuators are also used in automated packaging machinery to move and position products for packing. Their high speed and reliable performance make them ideal for repetitive packaging tasks.
5. Robotics
In some robotic systems, pneumatic actuators are used to provide movement and flexibility. They can be used for tasks like gripping, rotating, and positioning in automated robotic arms.
Benefits of Pneumatic Actuators
Pneumatic actuators offer numerous benefits that make them a popular choice for industrial automation. Some of the key advantages include:
1. Cost-Effective
Pneumatic actuators are generally more affordable than their electric or hydraulic counterparts. They are simple in design and construction, making them less expensive to manufacture and maintain.
2. High-Speed Performance
Pneumatic actuators are capable of delivering rapid motion, making them ideal for applications that require fast and repetitive movement. This makes them essential in high-speed automation processes such as packaging, material handling, and valve control.
3. Durability and Reliability
Built to withstand harsh industrial environments, pneumatic actuators are known for their durability and reliability. They can function in extreme temperatures, corrosive atmospheres, and other challenging conditions. Their long lifespan and low maintenance requirements further enhance their appeal.
4. Safety
Pneumatic actuators are inherently safer to use in environments where flammable gases or other volatile substances are present. Since they rely on compressed air rather than electricity or hydraulic fluids, the risk of sparks, leaks, or fires is significantly reduced.
5. Energy Efficiency
While pneumatic actuators require a continuous supply of compressed air, they are generally energy-efficient. Modern systems often incorporate air-recycling mechanisms that reduce overall air consumption and energy costs.
6. Flexibility
Pneumatic actuators are highly flexible in terms of customization and adaptability. They can be designed to meet specific application requirements, such as varying force levels, stroke lengths, and motion types. This makes them suitable for a wide range of industries and applications.
Conclusion
Pneumatic actuators are a critical component in industrial automation, providing efficient and reliable control over mechanical movements. Their versatility, combined with their cost-effectiveness, high-speed performance, and durability, makes them a preferred choice across many industries. Whether automating valves, controlling dampers, or moving materials, pneumatic actuators offer a powerful solution for achieving precise and reliable automation.
Understanding the different types, uses, and benefits of pneumatic actuators can help industries make informed decisions when selecting the right actuator for their needs. As technology continues to advance, pneumatic actuators will likely remain a key player in the automation landscape, driving efficiency and productivity across various sectors.
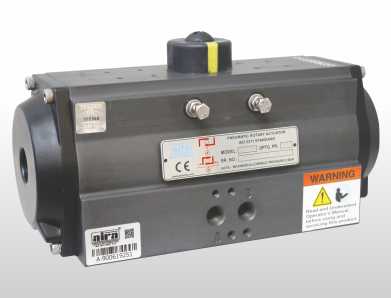