In the world of construction, equipment downtime is a nightmare. One broken-down equipment can trigger a domino effect, causing delays, lost wages, and the possibility of missing critical project deadlines. How do you avoid this? Simple: preventive maintenance.
Construction projects rely heavily on equipment to keep things moving. From bulldozers to cranes, the equipment is the backbone of the entire operation. If one piece of equipment fails, it can stall progress, rack up unnecessary costs, and throw timelines out the window. Yet, far too often, the importance of regular upkeep is overshadowed by the pressure to meet deadlines or budget cuts.
This leads to reactive maintenance waiting for equipment to break before fixing it which is more expensive and time-consuming in the long run. However, there’s a better way. Preventive maintenance (PM) is a proactive approach that ensures your equipment stays in optimal condition. It keeps things running smoothly, reduces the chances of breakdowns, and ultimately saves you money.
But with construction equipment becoming more complex, technology has stepped in to make the process smarter. From digital logs to construction equipment maintenance software, advanced tools now simplify preventive maintenance, making your equipment management more efficient and less error-prone.
What is Preventive Maintenance for Construction Equipment?
Preventive maintenance (PM) is like preemptive healthcare for your equipment.” It’s about regularly scheduled checks and repairs that ensure equipment doesn’t fail unexpectedly. Just like you’d visit the doctor for a routine checkup to catch any potential health issues early, PM allows you to see the problems before they become catastrophic.
Why It’s Vital
Preventive maintenance ensures that your equipment runs efficiently, reduces the need for expensive repairs, and helps avoid downtime that could halt construction progress. The key tasks include routine inspections, fluid changes, part replacements, and calibrations. These regular checkups help you spot wear and tear, catch problems early, and fix them before they cause serious disruptions.
Traditional vs. Tech-Enhanced
Traditionally, construction companies relied on manual tracking systems, like logbooks and spreadsheets, to document maintenance activities. While this worked, it was prone to errors, inconsistencies, and lack of visibility. Today, modern technology like construction equipment maintenance software has revolutionized how we approach PM. These software solutions offer automated scheduling, track maintenance history, and even send alerts for upcoming maintenance tasks.
The Core Benefits of Preventive Maintenance
1. Cost Savings:
You might ask: “How does spending more time on maintenance save me money?” The simple truth is that regular maintenance is far cheaper than expensive repairs or equipment replacements. Neglecting to fix a small issue can result in much larger, more costly problems. For instance, replacing a worn-out hydraulic pump is significantly cheaper than fixing a whole broken hydraulic system.
2. Reduced Downtime
Planned maintenance means less unplanned downtime. If your equipment is always in working order, there’s less chance it will break down during a critical task. This keeps your team moving and prevents delays, helping you meet deadlines without scrambling to fix last-minute failures.
3. Increased Equipment Lifespan
Regular maintenance doesn’t just prevent breakdowns it extends the lifespan of your equipment. Think of it like maintaining your car. Regular oil changes, tyre checks, and brake replacements keep your vehicle running smoothly for years. The same concept applies to construction equipment. By replacing worn parts and addressing minor issues early, you avoid the need for costly replacements and get more life out of your equipment.
4. Enhanced Safety
A well-maintained piece of equipment is a safer piece of equipment. Faulty equipment can pose serious risks to operators, workers, and the surrounding job site. Regular maintenance ensures that everything from brakes to hydraulic systems functions properly, preventing accidents that could result in injury or worse.
4. Key Tasks in Preventive Maintenance for Construction Equipment
The key to effective preventive maintenance is consistency. Below are the major tasks that should be regularly performed:
1. Routine Inspections
Think of this as giving your equipment a physical exam. A thorough inspection examines all critical components, like the engine, hydraulic systems, tyres, and fuel lines. Inspections help identify any potential issues before they escalate into costly repairs. It’s essential to catch problems early when they’re small and manageable.
2. Fluid and Part Checks
Fluids like engine oil, coolant, and hydraulic fluid are essential for properly functioning construction equipment. Regular checks ensure optimal fluid levels, preventing parts from grinding to a halt. Likewise, worn-out components like belts, filters, and hoses should be replaced before they cause a breakdown.
3. Lubrication
Proper lubrication is key to preventing friction and wear. Whether it’s the moving parts of an excavator’s arm or the wheels of a bulldozer, keeping everything properly lubricated ensures smooth operation and extends the life of the parts.
4. Cleaning and Calibration:
Equipment is often exposed to dirt, dust, and debris, clogging vital parts. Regular cleaning helps prevent this buildup and ensures that components function at their best. Additionally, regular equipment calibration ensures that it operates efficiently and safely.
Why Software Could Help
You might wonder, “How do I keep track of all these tasks?” Many teams now use construction equipment maintenance software to organize and automate their maintenance schedule. The software can track fluid levels, part replacements, and inspections and provide reminders so nothing falls through the cracks. It’s like having a personal assistant for your fleet of equipment.
The Future of Construction Equipment Maintenance
Emerging Trends
The construction industry is moving towards predictive maintenance, where data and equipment learning are used to forecast equipment failures before they happen. By analyzing equipment performance, these technologies predict when maintenance is required, reducing the risk of breakdowns and improving project timelines.
Long-Term Benefits
Technology is not just about saving time now, it’s about preparing for the future. Adopting a tech-driven maintenance approach ensures fewer breakdowns, greater safety, and a more efficient construction process in the long run.
Conclusion
Preventive maintenance is essential for keeping your equipment in optimal condition, avoiding costly breakdowns, and ensuring the smooth running of your projects. Whether managing one piece of equipment or an entire fleet, staying proactive with maintenance will save you time, money, and hassle.
As the construction industry evolves, embracing technology like construction equipment maintenance software will continue to play a key role in enhancing equipment management and ensuring long-term project success.
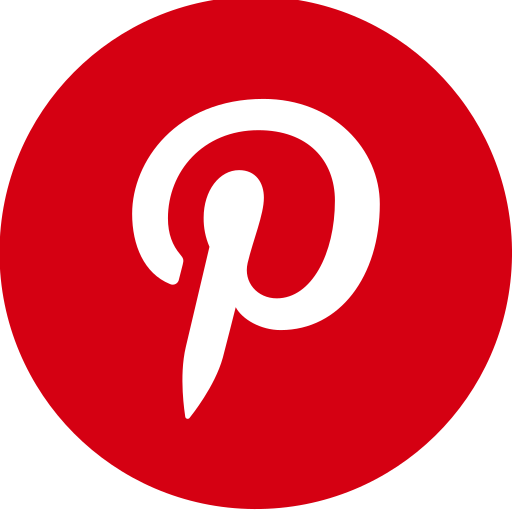