Tunneling and digging through rock, soil, or urban environments requires skilled handling, special equipment, and adjustments to different ground types. Mobile cranes form essential tools for underground work and also handle restricted tunnel spaces. These machines assist more than lifting operations because they help build tunnel boring machines (TBMs) while setting up structural linings and handling critical logistics tasks. Mobile cranes operate where regular cranes cannot, which makes them essential for modern tunneling operations.
The Design of Tunnel-Ready Mobile Cranes
Underground mobile cranes function as advanced mechanical solutions for restricted areas. These underground cranes differ from regular cranes because they are small in size and can easily be disassembled and reassembled. Cranes can use telescoping and articulating booms to perfectly reach and move around spaces within tunnels as well as equipment. Electric and hybrid power systems decrease emissions in poor ventilation areas where they operate.
The rubber tires or tracks help stabilize cranes on rough terrain while hydraulic outriggers help them to secure their position without taking up much space. Mobile cranes have digital control systems that let operators move loads through remote setups or small onboard operating stations. Each part of the equipment is made to endure humidity, dust, and ground vibrations since they often appear at tunneling worksites. For a project’s specific requirements, a company can reach out to a trusted supplier or official manufacturer that can provide a mobile crane for sale tailored for their project.
Mobile Cranes and TBM Installation
Decomposing and installing a heavy TBM machine, a cylindrical behemoth weighing hundreds of tons, rates as one of tunneling’s most intricate operations. Mobile cranes support this task by gently placing the TBM parts such as the cutter head, drive units, and trailing gear in their proper positions. In segmented tunnels, cranes work in phases: first, they disassemble and transport the TBM components through completed tunnel sections, then reassemble them at the new launch point.
The team needs to position and align heavy parts using very small movements for the hydraulic lines, electrical wiring, and bolt connections. Load moment indicators and anti-sway systems help stable cranes handle different part shapes during operation. Their ability to operate in low-headroom conditions allows TBMs to be constructed underground, eliminating the need for massive launch pits.
Installing Tunnel Segment Linings
After TBM progression the hollow space needs prompt sealing using precast concrete or steel segments. Mobile cranes perform their assigned task effectively and repeatedly without causing harm. Heavy transport vehicles drop segments one at a time which workers need to set against tunnel walls with high position accuracy. Cranes with robotic systems make the work easier by automatically controlling the grip force and orientation to prevent damage to the segment edges. The cranes function side by side at curved tunnel sections to place segments and supply raw materials at the same time. TBM operations depend on fast and accurate lining installation to stay on schedule because any delays here block the whole tunneling work.
Multifunctional Roles in Tunnel Logistics
Mobile cranes provide value for tunnel projects and many other construction activities beyond their role in TBM operations. Mobile cranes handle all shipping work in underground sites by moving tools and equipment to different positions. Cranes remove debris from the project area with their clamshell bucket or grappling devices while keeping drilling operations uninterrupted.
These machines help with emergencies by bringing out broken equipment and by installing temporary stabilization structures in unsafe areas. During maintenance breaks smaller cranes on rail carts and platform units access the TBM cutter heads to remove damaged disc cutters or scrapers. Specialized machines get replaced with one crane because they can handle different tasks for better use of space and financial resources.
Safety and Adaptability Underground
Operating cranes in tunnels brings special safety risks like poor visibility and nearness to working machinery. Every crane lift follows safety rules which include lowering weight limits to deal with uneven ground and using LiDAR sensors to avoid hitting things. Operators depend on all-direction cameras and sensing systems rather than eyesight.
Air quality monitoring systems check that diesel-powered crane exhaust stays below safety limits while using fire-resistant hydraulic fluids lowers fire risk. The field location serves as the primary setting for crane maintenance because taking these enormous machines back to the surface proves difficult. Additionally, crews train for scenarios like power failures, where backup battery systems take over to safely lower suspended loads
Innovations Shaping the Future of Tunnel Crane Technology
Tunneling project changes push mobile crane manufacturers to develop improved equipment. Semi-automated cranes in the form of Automaton systems perform basic lifting tasks without human control to bring lower operational expenses and fewer mistakes. Wireless load monitoring systems send accurate updates about equipment performance directly to surface operations for scheduled maintenance updates. Technology upgrades give electric cranes enough battery power to complete work shifts. Lightweight composite materials allow heavier loads for mobile cranes without needing additional expansion. Advanced AI systems could efficiently manage groups of crane operations to prevent delays and optimize their movements in real time. These improvements will make mobile cranes irreplaceable assets of underground construction operations.
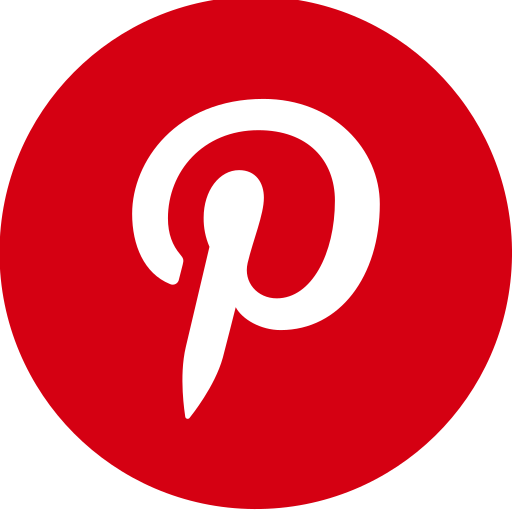