Establishing an ointment manufacturing plant requires precision, efficiency, and adherence to quality standards. One of the most critical aspects of setting up such a plant is selecting the right machinery. The choice of equipment impacts production efficiency, product quality, and compliance with regulatory standards. This article provides a comprehensive guide on how to choose the right machinery for an ointment plant.
1. Understanding the Manufacturing Process
Before selecting machinery, it is essential to understand the ointment manufacturing process. The typical production process includes:
Weighing and Mixing – Raw materials are measured and blended to form a uniform mixture.
Homogenization – Ensures even distribution of ingredients to achieve a smooth texture.
Heating and Cooling are required to achieve the desired viscosity and consistency.
Filling and Packaging – The final product is filled into tubes, jars, or bottles and sealed.
Labeling and Quality Control – Ensures compliance with regulations and branding requirements.
Understanding these steps helps in selecting machinery suited for each stage of production.
2. Key Factors to Consider When Choosing Machinery
Selecting the right machinery requires careful consideration of multiple factors:
a. Production Capacity
Determine the scale of production before investing in machinery. Whether you need a small, medium, or large-scale production setup will influence the size Ointment Plant and type of machines you require. Choose machines that align with your daily production goals.
b. Compliance with Regulatory Standards
Ointment manufacturing is subject to stringent regulatory requirements, including Good Manufacturing Practices (GMP), the FDA, and ISO certifications. Ensure that the machinery meets these compliance standards to avoid legal issues and maintain product quality.
c. Automation Level
Modern manufacturing plants rely on automation to improve efficiency. Choose between:
Manual Machines – Suitable for small-scale production but labor-intensive.
Semi-Automatic Machines – Offer a balance between automation and manual operation.
Fully Automatic Machines – Ideal for large-scale production, reducing human intervention and increasing consistency.
d. Material and Build Quality
Ointment machinery should be made of high-grade stainless steel to prevent contamination and ensure durability. Look for machines with corrosion-resistant and easy-to-clean surfaces.
e. Flexibility and Scalability
Select machines that allow flexibility for producing different formulations. Scalability is crucial if you plan to expand production in the future.
3. Essential Machinery for an Ointment Plant
Each stage of ointment production requires specialized machinery. Here are the key machines:
a. Mixing and Homogenization Equipment
These machines mix and homogenize ingredients to create a uniform texture. Common types include:
Vacuum Homogenizer Mixer – Ensures thorough mixing and eliminates air bubbles.
High-Speed Dispersers – Ideal for blending active ingredients uniformly.
Planetary Mixers – Used for precise mixing of viscous ointments.
b. Heating and Cooling Systems
Ointments require controlled temperature processing. Equipment includes:
Heating Kettles – Used for melting and heating ingredients.
Cooling Tanks – Helps achieve the desired viscosity.
c. Filling and Sealing Machines
Filling equipment varies based on the type of packaging. Options include:
Tube Filling Machines – For ointments packed in tubes.
Jar and Bottle Filling Machines – Used for cream and gel-based products.
Sealing Machines – Ensures airtight packaging to maintain product integrity.
d. Labeling and Packaging Equipment
To ensure professional packaging, use:
Labeling Machines – For automatic application of labels.
Cartoning Machines – For packing tubes, bottles, or jars in boxes.
e. Quality Control and Inspection Systems
Quality assurance is crucial in pharmaceutical production. Essential systems include:
Metal Detectors – To detect contaminants.
Viscosity Testers – To check the consistency of the ointment.
Microbial Testing Equipment – Ensures product safety.
4. Budget Considerations
Investing in the right machinery requires careful budget planning. Consider:
Initial Investment vs. Long-Term Gains – Higher-quality machines may cost more but offer better efficiency and longevity.
Maintenance Costs – Choose machines with lower maintenance requirements to minimize operational costs.
Energy Consumption – Opt for energy-efficient machines to reduce overhead costs.
5. Supplier and After-Sales Support
Choosing a reliable supplier is as important as selecting the machinery. Ensure the supplier:
Offers warranty and after-sales service.
Provides training for machine operation.
Has readily available spare parts.
Conclusion
Selecting the right machinery for an ointment manufacturing plant requires thorough research and planning. By considering production capacity, regulatory compliance, automation levels, material quality, and budget, you can invest in the most suitable equipment for your needs. A well-equipped ointment plant ensures efficiency, consistency, and high-quality products, positioning your business for long-term success.
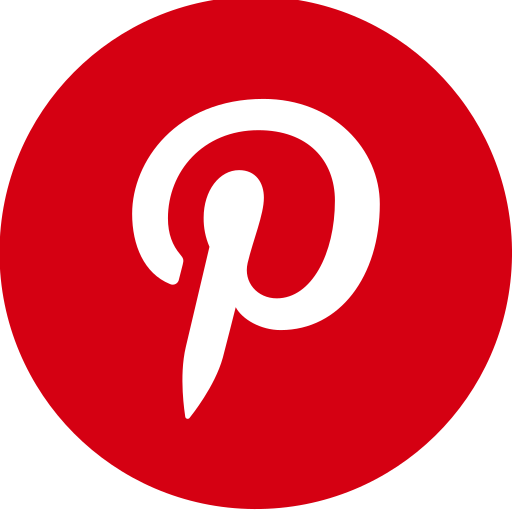