In the modern manufacturing world, producing high-quality products quickly and efficiently is essential for businesses aiming to stay competitive. High volume injection molding has emerged as one of the most effective methods for large-scale production, offering a balance of precision, cost-effectiveness, and speed. This manufacturing technique is widely adopted across various industries, from automotive to medical devices, electronics, and consumer goods, due to its remarkable ability to produce large quantities of identical parts with minimal waste.
In this article, we’ll explore why high volume injection molding is the ideal solution for businesses seeking to optimize their manufacturing processes, improve product consistency, and scale production to meet demand.
Understanding High Volume Injection Molding
High volume injection molding is a manufacturing process that involves injecting molten plastic into custom-designed molds to produce large quantities of identical parts. The process works by applying high pressure to force the molten plastic into the mold cavity, where it cools and solidifies into the desired shape.
This method is well-suited for mass production because it allows for continuous production cycles, meaning that once the mold is designed and created, the system can run almost autonomously, producing hundreds to thousands of parts every day with little downtime.
Key Advantages of High Volume Injection Molding
1. Cost Efficiency at Scale
One of the main reasons manufacturers opt for high volume injection molding is its cost efficiency. While the initial setup, particularly the cost of designing and creating the mold, can be high, the per-unit cost significantly decreases with larger production runs. This results in a lower cost per part as the production volume increases, making it an attractive option for businesses that need to produce large quantities of products. High volume injection molding becomes an economical choice for companies aiming to meet high demand without inflating production costs.
2. High Precision and Consistency
High volume injection molding ensures that every part produced is virtually identical to the next. Thanks to the advanced machinery and automated systems, the process offers exceptional precision, which is critical in industries such as automotive or medical devices, where even the smallest deviation in part design can affect performance and safety.
The consistency of injection molding is invaluable for manufacturers who require high-quality parts that meet strict tolerances. Because of its ability to replicate parts with incredible accuracy, manufacturers can rely on injection molding to maintain the highest standards of quality across their entire product line.
3. Wide Range of Materials
Injection molding is versatile when it comes to material selection. It can handle a variety of plastics, from standard thermoplastics to specialized compounds like elastomers and thermosets. Additionally, manufacturers can incorporate additives like colorants, flame retardants, or UV stabilizers into the materials to meet specific performance requirements, such as increased durability or resistance to harsh environments.
This material versatility makes high volume injection molding applicable across a wide range of industries, enabling manufacturers to produce everything from consumer products to intricate medical devices.
4. Fast Production Speeds
When it comes to mass production, speed is a crucial factor. High volume injection molding can produce thousands of parts per day, depending on the complexity of the design and the type of material used. Once the mold is ready, the production cycle can be automated to the point where parts are consistently produced in rapid succession.
This efficiency allows companies to meet tight deadlines and fulfill large orders quickly, giving them the flexibility to adjust production volumes based on changing market demands.
5. Reduced Waste and Environmental Impact
One of the significant advantages of high volume injection molding is its ability to reduce waste. The process is highly controlled, and any excess plastic material can often be reused in future production cycles. This is especially beneficial for companies looking to implement more sustainable manufacturing practices.
Additionally, because the molds are designed for durability and repeated use, the environmental impact is minimized compared to other manufacturing methods that may require more energy or generate more waste. For companies that prioritize sustainability, high volume injection molding offers a way to reduce their carbon footprint while maintaining efficient production.
6. Customization and Complex Designs
Although injection molding is associated with mass production, it is also capable of creating complex, customized designs. The molds can be engineered to accommodate intricate shapes, undercuts, or fine details, allowing manufacturers to produce parts that meet highly specific design criteria.
This flexibility makes injection molding ideal for industries that require both high-volume and custom-made products, such as the electronics or automotive industries, where parts often need to fit within a precise design framework.
Industries Benefiting from High Volume Injection Molding
1. Automotive Industry
The automotive industry relies heavily on injection molding to produce a vast array of parts, from exterior components like bumpers to interior features such as dashboard elements and connectors. Injection molding’s precision and speed make it an excellent choice for producing high-quality, durable components in large quantities.
2. Medical Device Manufacturing
In the medical device industry, where safety and consistency are of the utmost importance, high volume injection molding is used to produce parts for devices such as syringes, implants, and diagnostic equipment. The ability to meet stringent quality standards while maintaining cost-effectiveness is crucial in this field.
3. Consumer Electronics
The consumer electronics market also takes advantage of high volume injection molding to produce housings for devices such as smartphones, computers, and home appliances. The need for precise, durable components at a lower cost is a driving factor for manufacturers to choose injection molding.
4. Packaging
Packaging materials, such as bottles, containers, and caps, are often produced using high volume injection molding. The process is ideal for creating large quantities of uniform products with intricate designs, making it the preferred choice for packaging companies.
Conclusion:
High volume injection molding is a key player in the world of large-scale production, offering numerous benefits such as cost efficiency, high precision, speed, and material versatility. It allows businesses to scale production quickly and produce high-quality products that meet the demands of competitive industries. Whether you’re in automotive, medical devices, consumer goods, or packaging, high volume injection molding provides the efficiency and consistency required to meet high production demands while keeping costs under control.
As industries continue to evolve and demand more from manufacturers, high volume injection molding will remain a cornerstone of large-scale manufacturing, enabling businesses to create the parts they need with precision, speed, and sustainability.
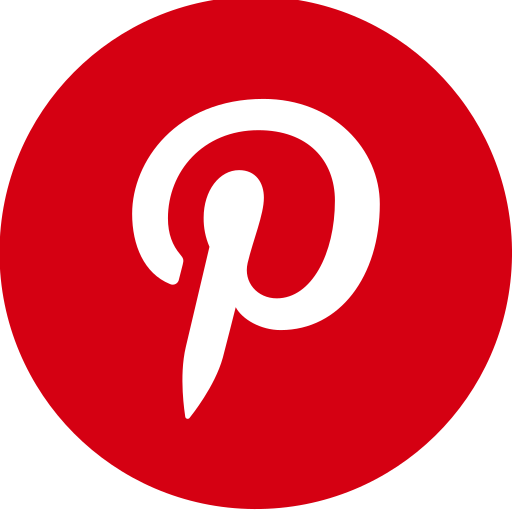